NUM begleitet die Entwicklung einer neuartigen Abrasiv-Wasserstrahlschneidanlage
Ein Start-up der TU Chemnitz bringt mit NUM das Abrasiv-Wasserstrahlschneiden mit Suspensionstechnik auf eine CNC-gesteuerte Werkzeugmaschine. Mit mehr Effizienz und höherer Qualität soll sich die Anlagentechnik als kaltes Schneidverfahren zwischen Laser und Injektor-Wasserstrahlschneiden platzieren. Für die bisher in der industriellen Fertigung so nicht bekannte Strahlerzeugung bietet eine flexible und offene Steuerung von NUM die optimalen Voraussetzungen.
„Unser Ziel war es, eine kompakte Abrasiv-Wasserstrahlschneidanlage auf Basis der Suspensionstechnik zu bauen, die deutlich leistungsfähiger und gleichzeitig effizienter als eine herkömmliche Wasserstrahlschneidmaschine mit Injektortechnik ist. Das ist uns gelungen“, sagt Markus Dittrich, Mitgründer und Geschäftsführer des Start-ups NOVAJET und derzeit noch wissenschaftlicher Mitarbeiter am Institut für Werkzeugmaschinen und Produktionsprozesse (IWP) an der TU Chemnitz. Entstehen soll eine Feinstrahlanlage, die auf Strahldurchmesser kleiner als 0,4 mm fokussiert und für die Herstellung präziser kleiner Bauteile aus schwer bearbeitbaren Materialien wie Keramik oder Hartmetall optimiert ist. Mit der Entwicklung haben die Gründer technisches Neuland betreten, eine Werkzeugmaschine in dieser Art gibt es noch nicht – und entsprechend auch keine fertige Steuerung. Nicht zuletzt weil Optimierungen und Hardwareänderungen im Laufe des Aufbaus der Prototypenanlage üblich sind, haben sich die Gründer für eine flexible und offene NUM-Steuerung entschieden.
Von der Injektor zur Suspensionstechnik
Begonnen hat es mit einem Forschungsprojekt zum 3D-Abrasiv-Wasserstrahlschneiden mit Strahldurchmessern von etwa 0,3 mm. „Wir haben festgestellt, dass die Schneidleistung des Strahles mit der herkömmlichen Injektortechnik exponentiell abnimmt, je kleiner wir den Strahldurchmesser machen. Zum Schluss konnten wir nur noch Dünnblech schneiden“, erläutert Markus Dittrich und liefert die technische Erklärung gleich mit: In herkömmlichen Abrasiv-Wasserstrahlanlagen wird das Wasser auf einen Druck zwischen 3‘000 und 6‘000 bar gebracht und durch eine Wasserdüse in eine Mischkammer geleitet. Dort entsteht ein Unterdruck, der trockenes Abrasiv aus einem Vorratsbehälter ansaugt und mit dem Wasserstrahl mitreisst. „Alleine das Beschleunigen des Abrasivs frisst rund 30 Prozent der ursprünglich ins Wasser eingebrachten Energie“, sagt Dittrich. Zudem bringt diese Art des Mischvorgangs viel Luft in den Strahl und verteilt das Abrasiv überwiegend am Strahlumfang. Beides mindert die Abtragsleistunga
Eine Alternative ist die Suspensionstechnik, eine Abrasiv-Wasserstrahlschneidtechnik, die bisher mehr für grobe Anwendungen, beispielsweise in der Kraftwerksdemontage, eingesetzt wird. Im Prinzip werden dabei Wasser und Abrasiv im ruhenden Zustand zu einer Suspension gemischt, in einem Hochdruckbehälter unter Druck gesetzt, zur Schneiddüse geleitet und dort zu einem Hochgeschwindigkeits-Schneidstrahl ausgebildet. Dass diese Technik das Potenzial hat, auf einer Werkzeugmaschine eingesetzt zu werden, wurde in einem Folgeprojekt an der TU Chemnitz mit den industriellen Projektpartnern ANT AG und ATECH GmbH bereits nachgewiesen. „Leistungssteigerungen um bis zu 340 Prozent gegenüber dem Injektorverfahren sind möglich“, fasst Dittrich das Ergebnis zusammen. Praxisbezogener ausgedrückt: Mit einem Druck von 1‘400 bar wurde bei sonst gleichen Bedingungen in den Versuchen mehr als dreimal schneller und präziser geschnitten als mit der Injektortechnik mit 3‘000 bar. Und das auch in Keramik. Das liegt auch an der Strahlqualität, denn der Strahl ist luftfrei und das Abrasiv ist im Strahlkern verteilt. Selbst der wasserstrahltypische Winkelfehler ist beim Suspensionsschneiden deutlich kleiner und es wurden in Versuchen bereits Strahldurchmesser von 0,2 mm realisiert. Gefördert durch das Bundesministerium für Wirtschaft und Energie und den Europäischen Sozialfonds ist aus dem Projekt mittlerweile ein Start-up geworden, das seit August als Firma agiert und ab Anfang nächsten Jahres mit seiner Anlagentechnik am Markt auftreten wird.
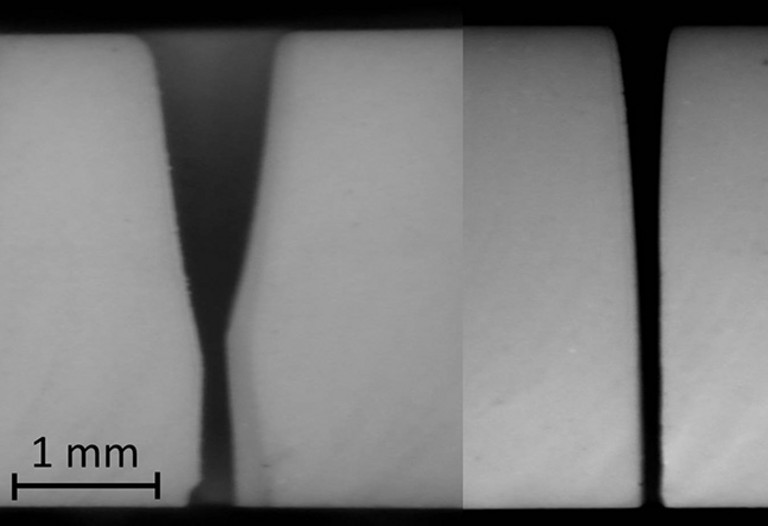
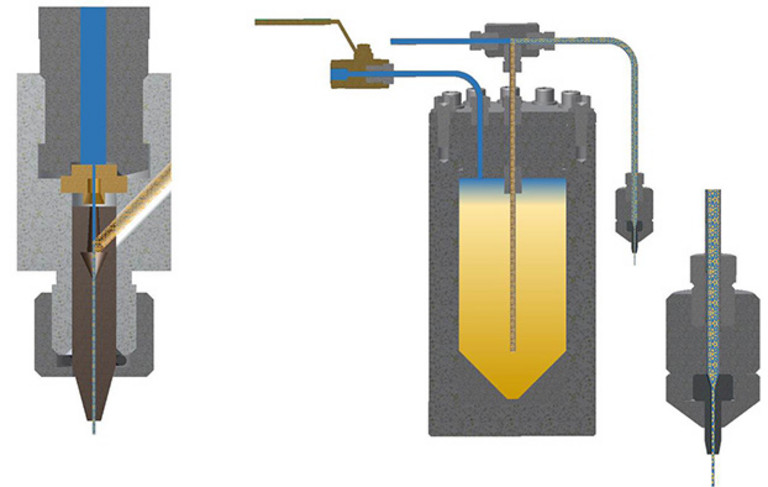
Anlage für die Industrie
Bis dahin wird an der Anlage weiter optimiert. Im Entwurf und nach den ersten Ausbaustadien baut die Anlage sehr kompakt. Alle Komponenten, von der Hochdruckpumpe über den Hochdruckbehälter bis zum Arbeitstisch und Schneidsystem, sind in einem Rahmen hinter einer gemeinsamen Verkleidung untergebracht. Die Maschine arbeitet mit 1‘500 bar Wasserdruck, und im Hinblick auf die Präzisionsfertigung kleiner Teile reicht ein Arbeitstisch von 350 mm x 510 mm aus. Der Hochdruckbehälter ist so ausgelegt, dass mit je einer Füllung und einem Strahldurchmesser von 0,4 mm rund 20 Minuten reine Schneidzeit bedient werden können. Danach wird der Behälter in der Endausbaustufe automatisch entlastet, neu befüllt und wieder mit Druck beaufschlagt.
Im Hochdruckbereich ist die Anlage allerdings komplizierter aufgebaut, als es das Prinzip der Suspensionstechnik vermuten lässt. So werden ein Hauptströmungsweg mit reinem Wasser von der Hochdruckpumpe und ein Nebenströmungsweg für die Suspension aus dem Hochdruckbehälter gekoppelt. Die homogene Zusammensetzung des Strahles erfordert aber eine aufwändigere Regelungstechnik. „Wir haben weit mehr als eine Handvoll Ventile, die aufeinander abgestimmt sein müssen. Dazu kommt eine integrierte Hochdruckpumpe. Und wir haben Prozessüberwachungssysteme, die sowohl den Strahl und die Abrasivmischung selbst als auch den Hochdruckbehälter überwachen“, sagt Markus Dittrich. Diese Überwachungssysteme gibt es bei der Injektortechnik so nicht und folglich gibt es dafür auch keine fertige Steuerung, die die Signale der Überwachungssysteme in regelnde Inputs für das Gesamtsystem umwandelt.
„Für die Auswahl der Steuerung war es uns sehr wichtig, dass vom Niederdruckwasser am Anfang über die Achsensteuerung und die automatische Befüllung bis zum Schneidkopf am Ende alles über eine Steuerung läuft. Im ungünstigen Fall liefert die Schneidkopfüberwachung nämlich ein Signal, das ein Nachregeln an der Hochdruckpume erfordert. Diese Verknüpfungen im Hintergrund aufzubauen, ist für unsere Technologie sehr relevant“, sagt Markus Dittrich.
Eine NUM-Steuerung habe sich dabei angeboten, denn erstens sind NUM-Steuerungen in den Schleifmaschinen im anvisierten Markt der Hochleistungswerkstoffindustrie standardmässig vertreten, zweitens gibt es bereits Wasserstrahlschneidanlagen mit NUM-Steuerungen im Markt, sodass entsprechend konfigurierte Bausteine für das Wasserstrahlschneiden verfügbar sind, und drittens liefert NUM ein Komplettpaket vom PC über das Panel und die CNC-Steuerung bis zu den Antrieben und Motoren. Nicht zu vergessen die Unterstützung durch Ingenieursdienstleistungen.
Positive Erfahrungen mit der Inbetriebnahme
Die Entscheidung hat sich bereits in der Aufbauphase als richtig erwiesen. Zur Inbetriebnahme der Motoren war ein NUM-Mitarbeiter zwei Tage in Chemnitz, sodass die Antriebe schnell installiert waren. Mit der Kenntnis aus einer einwöchigen Schulung konnten die Gründer die restliche Inbetriebnahme innerhalb von 14 Tagen dann alleine erledigen. „Wir hatten aber immer die Möglichkeit der telefonischen Unterstützung. Die Kollegen haben sich dann per TeamViewer bei uns ins System eingeloggt. Wir konnten relativ problemlos alle Schwierigkeiten beseitigen“, sagt Stefan Seidel, der für den technischen Part zuständige Mitgründer. Und in der Aufbauphase der Anlage erweist sich auch die Programmierung der Reaktionszyklen unkompliziert. Im Vordergrund aber steht die Möglichkeit, direkt auf die NC der Steuerung zugreifen zu können.
„Während der Inbetriebnahme fallen uns immer wieder Details auf, die wir ändern oder anpassen“, sagt Dittrich. „Dann müssen wir natürlich auch die Steuerung anpassen. Wenn wir da auf einen Steuerungshersteller angewiesen wären, der sich jede Änderung fürstlich bezahlen lassen würde oder dort grosse Iterationsschleifen notwendig wären, dann wären wir im Rahmen des Projekts aufgeschmissen.“
(September 2019)