NUM assists development of innovative abrasive waterjet cutting system
With the help of NUM, a start-up company of Chemnitz Technical University is bringing abrasive waterjet cutting with suspension technology to the CNC machine tool market. Offering higher efficiency and quality than conventional waterjet cutters, the technology looks set to position itself as a cold cutting process between laser and injector waterjet cutting. A flexible and open control system from NUM provides the optimum conditions for abrasive beam generation – a cutting technology that until now has not been seen in industrial manufacturing applications.
“Our goal was to build a compact abrasive waterjet cutting system based on suspension technology that is significantly more powerful and at the same time more efficient than a conventional waterjet cutting machine with injector technology. We have succeeded“, says Markus Dittrich, co-founder and managing director of the NOVAJET start-up and currently still a research associate at the Institute for Machine Tools and Production Processes (IWP) at Chemnitz Technical University. The aim is to develop a fine blasting system that focuses on beam diameters smaller than 0.4 mm and is optimized for the production of small precision components from difficult-to-machine materials such as ceramics or tungsten carbide. With this development, the founders have broken new ground in technology – a machine tool of this kind does not yet exist and the control system is currently still being developed. Due to the fact that optimizations and hardware changes are quite common during the course of setting up any prototype system, the founders opted for a flexible and open NUM control system.
From injector to suspension technology
It began with a research project on 3D abrasive waterjet cutting with jet diameters of about 0.3 mm. “We have found that the cutting power of the jet with conventional injector technology decreases exponentially the smaller we make the jet diameter. In the end, we could only cut thin sheet metal“, explains Markus Dittrich and provides the technical explanation at the same time: In conventional abrasive water jet systems, the water is brought to a pressure of between 3,000 and 6,000 bar and fed through a water nozzle into a mixing chamber. This creates a vacuum that sucks dry abrasive from a storage container and carries it along with the water jet. “Accelerating the abrasive alone consumes around 30 percent of the energy originally introduced into the water“, says Dittrich. In addition, this type of mixing process introduces a lot of air into the jet and mainly distributes the abrasive around the circumference of the jet. Both reduce the removal rate.
An alternative is suspension technology, an abrasive water jet cutting technology that has so far been used more for coarse applications, for example in power plant dismantling. In principle, water and abrasive are mixed to form a suspension when at rest, pressurized in a high-pressure container, fed to the cutting nozzle and formed into a high-speed cutting jet. That this technology has the potential to be used on a machine tool has already been proven in a follow-up project at Chemnitz Technical University with industrial project partners ANT AG and ATECH GmbH. “Performance increases of up to 340 percent compared to the injector process are possible“, Dittrich summarizes the result. In practical terms: with a pressure of 1,400 bar and otherwise the same conditions, the tests showed that cutting was more than three times faster and more precise than with the injector technology at 3,000 bar. And also in ceramics. This is also due to the jet quality, because the jet is air-free and the abrasive is distributed in the jet core. Even the typical water jet angle error is significantly smaller during suspension cutting and jet diameters of 0.2 mm have already been achieved in tests.
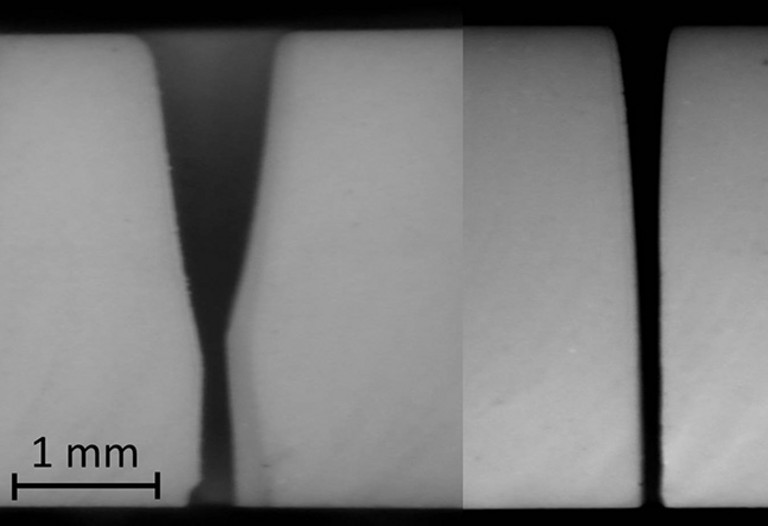
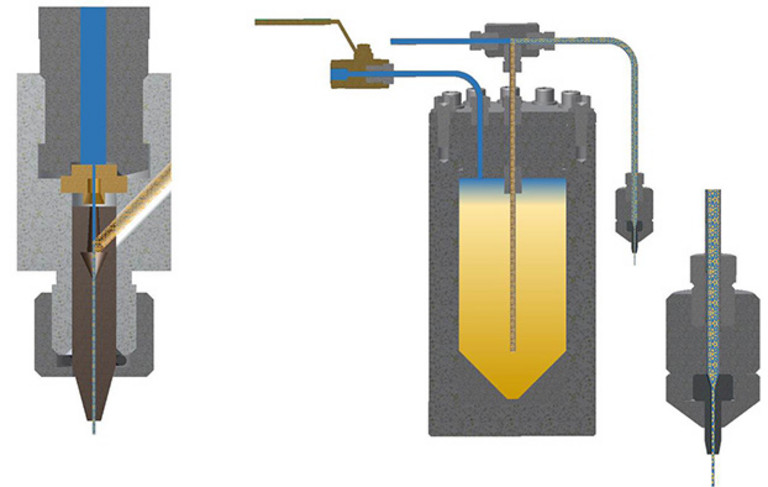
Machine for industry
The system is about to be further optimized. The plant is very compact in design and after the first expansion stages all components – from the high-pressure pump to the high-pressure tank to the worktable and cutting system – are housed in a single frame behind a common cladding. The machine operates at 1,500 bar water pressure, and a 350 mm x 510 mm worktable is sufficient for precision manufacturing of small parts. The high-pressure tank is designed in such a way that with a single filling and a jet diameter of 0.4 mm, around 20 minutes of pure cutting time can be achieved. Then, in the final development stage, the container will be automatically unloaded, refilled and pressurized again. In the high-pressure range, however, the system is more complicated than the principle of suspension technology would suggest. For example, a main flow path with pure water from the high-pressure pump is coupled with a secondary flow path for the suspension from the high-pressure tank. However, the homogeneous composition of the jet requires more complex control technology. “We have far more than a handful of valves that have to be matched to each other. There is also an integrated high-pressure pump. And we have process monitoring systems that monitor both the jet and the abrasive mixture itself as well as the high-pressure tank“, says Markus Dittrich. These monitoring systems do not exist in injector technology and consequently there is no ready-made control system that converts the signals from the monitoring systems into regulating inputs for the entire system.
“For the selection of the control system, it was very important to us that everything from the low-pressure water at the beginning to the axis control and the automatic filling up to the cutting head at the end runs via a control system. In the worst case, the cutting head monitoring provides a signal that requires readjustment at the high-pressure pump. Establishing these links in the background is very relevant for our technology“, says Markus Dittrich.
NOVAJET elected to use NUM’s CNC platform for several reasons. Firstly, NUM controls are standard in the grinding machines in the targeted market of the high-performance materials industry; secondly, there are already waterjet cutting systems with NUM controls on the market, which means that appropriately configured components are available for waterjet cutting; and thirdly, NUM supplies a complete package from the PC to the panel and the CNC control to the drives and motors. Not forgetting the support of engineering services.
Positive experience with commissioning
The decision to choose NUM proved to be the right one, even during the start-up phase. A NUM employee spent two days in Chemnitz to commission the motors, so that the drives were quickly installed. With the knowledge gained from a one-week training course, the founders were able to complete the remaining commissioning within 14 days on their own. “However, we always had the option of telephone support. The colleagues then logged on to the system using TeamViewer. We were able to eliminate all difficulties relatively easily“, says Stefan Seidel, the co-founder responsible for the technical part. And during the construction phase of the plant, the programming of the reaction cycles also proved to be uncomplicated. However, the focus is on the option of direct access to the NC of the control system.
“During commissioning, we kept noticing details that we needed to change or adapt“, says Dittrich. “Then, of course, we also had to adapt the control. If we had been forced to rely on a controller manufacturer who charged for every change or who required large iteration loops, then the project would have been up a creek without a paddle“, sums up Markus Dittrich.
(September 2019)