Industry 4.0 - TechniControl and NUM implement link between ERP system and production
Industry 4.0 is not new territory for TechniControl and NUM. TechniControl stands for top technology in process automation and production control, NUM represents CNC high-end applications. With these qualified prerequisites, a connection to an ERP system with fully automatic data generation of the ISO code and subsequent transmission (NUM IsoTrans) to the CNC machine could be realized. At the same time, the processing sequence is optimized, production speed is increased and waiting times are noticeably reduced.
TechniControl Informatik GmbH offers complete systems as well as individual solutions and services for the manufacturing industry. For almost 20 years, TechniControl and its employees have been controlling, optimizing and visualizing industrial processes at SCADA level. The company is based in Schmalenberg, south of Kaiserslautern (Germany). Many years of experience and the use of sophisticated software modules enable the developers to implement even complex special solutions in the shortest possible time. The aim of the company is to offer an efficient and powerful software structure for the realization of integrated production processes, fully automatically down to batch sizes of one.
TechniControl and NUM have implemented the link between ERP system and CNC machine. The automatic processing of the data records takes place in the background while the machine is running. The individual machining operations on the current workpiece are graphically displayed to the operator by the control system software. The detailed sequence takes place as follows: From the data record for a production order, TechniControl generates a job file for each individual part directly from the order pool of the ERP system and transfers it just-in-time to the IPC (industrial PC) of the machine. This job file is used to generate the ISO code for the NUM Flexium+ machine control system. The job file of the control system is analyzed fully automatically. In addition, an optimized processing sequence is calculated from which the path-optimized ISO program code is generated. All processing steps can be flexibly combined by four defined basic geometries. The ISO code for the CNC machine is generated using NUM’s newly developed IsoTrans program and transferred from the postprocessor to the machine control via FXServer. One area where this approach comes into play is, for example, a waterjet cutting machine from STM Stein-Moser GmbH in Austria, which cuts insulation materials precisely and fully automatically. This is a 5-axis waterjet cutting machine with a NUM Flexium+ 68 CNC control and NUM industrial PC.
In the further processing process, the cut insulating and insulating materials are further processed together with other individual parts, some of which are manufactured in different production plants and different machines. Therefore, the accuracy of the machined workpieces and a fully automatic process for further processing are of utmost importance. On the basis of the order from the ERP system, TechniControl generates a unique ID number for quality assurance reasons and to ensure complete traceability of the product and applies it as a label to the individual parts.
The web optimization function has, among other things, a special function for avoiding double cuts and generates a continuous cutting path. Unnecessary cuts and superfluous repositioning of the cutting nozzle can thus be avoided, which guarantees an enormous reduction in processing time. Depending on the configuration and requirements, the optimum cutting path can be individually selected - down to a batch size of one - automatically using the NUM IsoTrans application. This modern communication technology networks the entire production process. There are no waiting times for the machine operator and no loss of time in the entire production process.

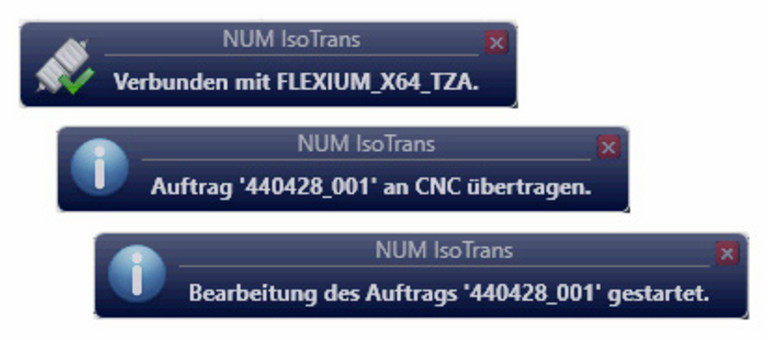
NUM IsoTrans monitors each workpiece from start to finish and sends feedback on the status of the job to the PCS (Process Control System). In the event of an error during machining, all messages that have occurred on the machine are sent to the PCS. The PCS uses this information to inform the operator of production progress and to enable an uninterrupted workflow. No user interface is visible in the production mode of NUM IsoTrans. The connection status is indicated by a tray symbol and the machine operator receives status messages of the current process steps via so-called “Balloon Tips”. The user interface can be opened via the tray icon and displays information about the immediately processed order as well as the next order that has already been prepared and, if necessary, transformed. The message history provides an overview of the last processed orders and events. General settings such as required directories, CNC program number etc. can be defined via a settings page. Technology data such as focus distance, maximum axis speed, Z position, cutting pressure and other settings can be defined via an additional tab.
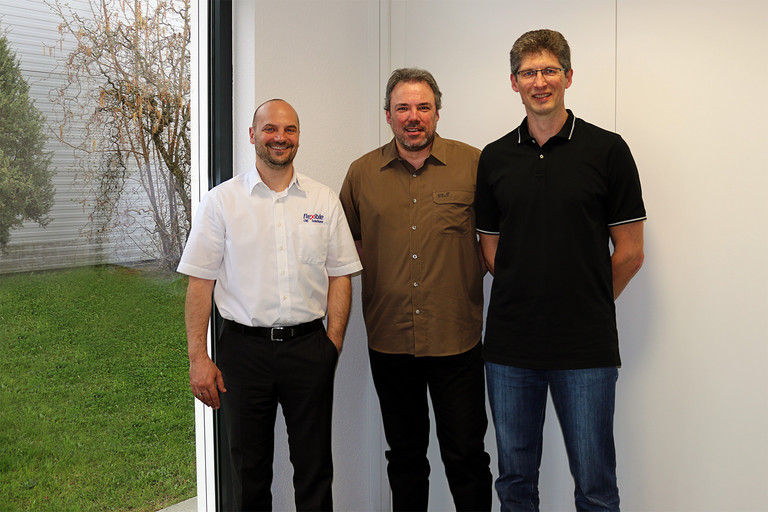
The starting point of the project was the requirement for individual production as well as the critical analysis and screening of the systems involved in the production process by TechniControl. Subsequently, possible solutions were discussed together with NUM and the project schedule was defined. Due to the open and professional communication, challenges could be overcome quickly and solved in a target-oriented way by both sides. “The performance efficiency of the machine could be significantly increased by optimizing machining”, says Stefan Velten, one of the two Managing Directors of TechniControl. Mr. Viktor Horn, second Managing Director of TechniControl, adds praisingly: “One highlight was the commissioning. Instead of the planned three days, commissioning could be carried out within half a day. A true example of commissioning.”
(September 2019)