Industrie 4.0 - TechniControl et NUM : Un lien entre le système ERP et la production
Pour TechniControl et NUM, Industrie 4.0 n’est pas un nouveau territoire. TechniControl offre une technologie de pointe en matière d’automatisation de processus et de contrôle de production; NUM, de son coté, est synonyme d’applications CNC haut de gamme. Grâce à ces deux acteurs, la connexion à un système ERP avec génération automatique du code ISO et transmission ultérieure (NUM IsoTrans) à la machine CNC a pu être réalisée. Une séquence de traitement optimisée, la rapidité de production augmentée et des temps d’attente sensiblement réduits en sont les bénéfices immédiats.
TechniControl Informatik GmbH offre des systèmes complets ainsi que des solutions et services individuels pour l’industrie manufacturière. Depuis près de 20 ans, la société basée à Schmalenberg, au sud de Kaiserslautern (Allemagne) et ses employés contrôlent, optimisent et permettent de visualiser les processus industriels au niveau SCADA (Systèmes de contrôle et d’acquisition de données). De nombreuses années d’expérience et l’utilisation de modules logiciels sophistiqués permettent aux développeurs de mettre en œuvre des solutions spécifiques, parfois même complexes, dans les plus brefs délais. L’objectif de l’entreprise est d’offrir une structure logicielle efficace et performante pour la réalisation de processus de production intégrés, entièrement automatisés jusqu’au niveau de la pièce individuelle.
TechniControl et NUM assurent le lien entre le système ERP et la machine CNC. Le traitement automatique des données s’effectue en arrière-plan pendant le fonctionnement de la machine. Les différentes opérations d’usinage sur la pièce en cours sont représentées graphiquement à l’opérateur par le logiciel du système de commande.
En partant des données d’un ordre de fabrication, TechniControl génère, pour chaque pièce individuellement, un fichier de travail issu des commandes enregistrées dans le système ERP et le transfère au moment voulu sur le PC industriel de la machine. Ce fichier de travail va servir à générer le code à destination du système Flexium+ qui contrôle la machine. Il est analysé de manière entièrement automatique, à la suite de quoi, une séquence de traitement optimisée est effectuée après laquelle un programme en code ISO optimisé est généré. Seules, quatre formes prédéfinies et paramétrables sont nécessaires pour décrire de manière flexible les différentes étapes du traitement. Le code ISO de la machine est alors généré à l’aide du récent programme NUM IsoTrans et est transféré à Flexium+ via FXServer. Un des exemples d’application récents est une machine de découpe au jet d’eau 5 axes de STM Stein-Moser GmbH en Autriche, équipée d’un Flexium+ 68 qui découpe, avec précision et de manière entièrement automatique, des matériaux d’isolation.
Au cours du processus de fabrication, les pièces découpées dans le matériel isolant sont assemblées avec d’autres pièces individuelles, dont certaines ont été fabriquées sur d’autres machines et dans différentes installations de production. C’est pourquoi la précision des pièces usinées et l’automatisation du processus de traitement ultérieur sont d’une importance capitale. Sur la base des commandes du système ERP, TechniControl génère, pour se conformer aux normes d’assurance qualité et assurer une traçabilité complète du produit, un numéro d’identification unique qui est appliqué sur les différentes pièces sous la forme d’une étiquette.
La fonction d’optimisation du programme a, entre autres, la particularité de générer un parcours de coupe continu pour éviter les doubles coupes. Les coupes inutiles ainsi que des repositionnements de la buse de découpe superflus peuvent ainsi être évités, ce qui garantit une importante réduction du temps de traitement. L’application NUM IsoTrans permet, en fonction de la configuration et des besoins, de sélectionner automatiquement la trajectoire de coupe optimale. Grâce à cette technologie de communication moderne, l’ensemble du processus de production est ainsi géré en réseau. Il n’y a pas de temps d’attente pour l’opérateur de la machine ni aucune perte de temps dans l’ensemble du processus de production.

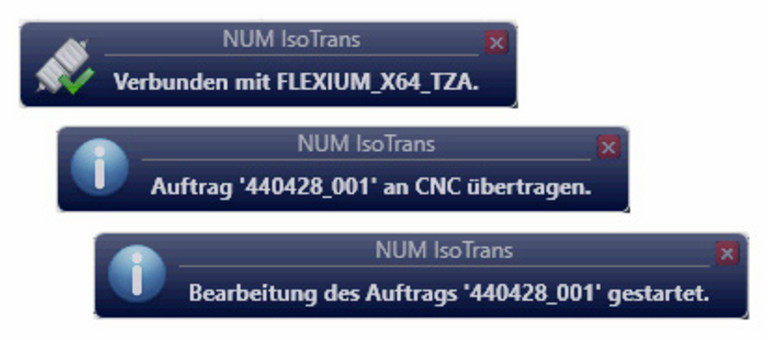
NUM IsoTrans surveille chaque pièce du début à la fin et envoie au système de contrôle du processus (PCS : Process Control System) des informations sur l’état du travail. En cas de problème en cours d’usinage, tous les messages survenus sur la machine sont envoyés au PCS. Le PCS utilise ces informations pour informer l’opérateur de l’état d’avancement de la production et pour permettre un flux de travail ininterrompu. Il n’y a aucune interface utilisateur visible dans le mode de production de NUM IsoTrans. L’état de la connexion est indiqué par un symbole et l’opérateur de la machine reçoit des messages d’état des étapes du processus en cours via des “Bulles d’état“. L’interface utilisateur peut être alors ouverte par un simple click sur une icône de la barre d’état et affiche alors les informations sur la commande immédiatement traitée ainsi que sur la commande suivante qui a déjà été préparée et, si nécessaire, optimisée. L’historique des messages fournit une synthèse des derniers ordres et événements traités. Les paramètres généraux tels que les répertoires, le numéro de programme de la CNC, etc. peuvent être définis sur une page de paramètres. Les données technologiques telles que la distance focale, la vitesse maximale de l’axe, la position Z, la pression de coupe et d’autres réglages peuvent être définis par un onglet supplémentaire.
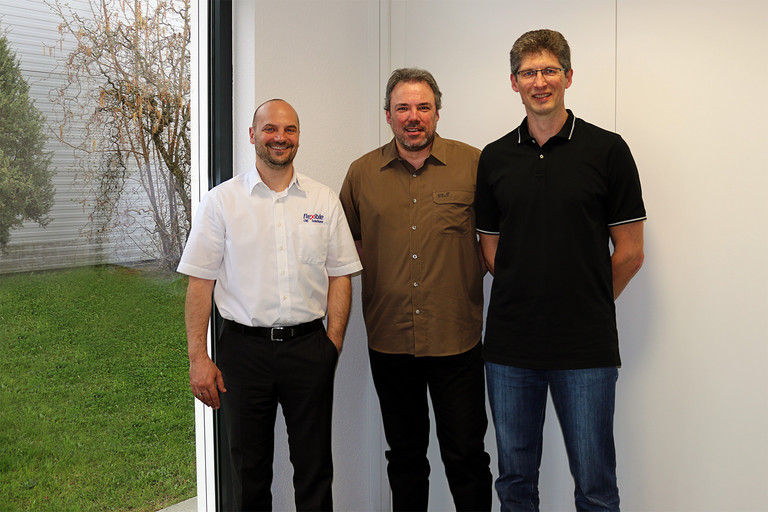
Le point de départ du projet était l’exigence d’une production individuelle ainsi que l’analyse critique et l’évaluation des systèmes impliqués dans le processus de production par TechniControl. Les solutions possibles ont ensuite été abordées avec NUM et un calendrier de projet défini. Grâce à une communication directe et efficace entre les équipes, les défis ont pu être rapidement surmontés et résolus de manière ciblée par les deux parties. « L’optimisation de l’usinage a permis d’augmenter considérablement l’efficacité des performances de la machine », explique M. Stefan Velten, l’un des deux directeurs de TechniControl. M. Viktor Horn, directeur général de TechniControl, ajoute avec satisfaction : « L’un des points forts à noter fût la mise en service. Au lieu des trois jours prévus, la mise en service a pu se faire en une demi-journée ; un véritable exemple. »
(Septembre 2019)