L’aggiornamento CNC personalizzato semplifica la tornitura asse dell’automotrice
Un aggiornamento completo di macchine utensili per la tornitura classica senza centri a elevata potenza consente a un produttore leader di assi per automotrice di semplificare notevolmente le operazioni di tornitura di precisione su elementi forgiati per asse. Un elemento chiave del progetto, gestito da APeC Integration Services, Inc, è il retrofit di controllo CNC personalizzato basato su una potente piattaforma Flexium di NUM.
Con sede a Wattsburg PA, APeC è un integratore di sistemi elettrici specializzato nell’aggiornamento delle macchine utensili con PLC moderni e sistemi di controllo CNC. Fondata nel 1989, l’azienda si è costruita una reputazione per consentire ai clienti di ottimizzare la durata e le prestazioni dei propri investimenti macchina. I servizi retrofit principali includono l’aggiornamento di servo, motori mandrino e unità, l’integrazione PLC e i comandi della macchina personalizzati e la sostituzione completa CNC.
Le macchine utensili di questo particolare progetto sono rettificatrici Landis senza centri a elevata capacità che utilizzano una mola ravvivabile e un ciclo di tornitura a immersione per creare profili di precisione sui perni dell’asse per automotrice. Durante la rettifica, sia il pezzo asse sia la mola ruotano nella stessa direzione, ovvero le due superfici si muovono in direzioni opposte al punto di contatto per un funzionamento più regolare. Una volta che la macchina è a regime, la mola viene alimentata, o ‘immersa’, nel pezzo ed entra in contatto continuo con un solo punto lungo la sua lunghezza. L’azione di immersione è controllata da una rettifica asse guidata da servo a diverse velocità, con punti di transizione monitorati da misurazioni continue. Un sistema di rettifica automatizzato a due assi con uno strumento a punta di diamante viene utilizzato per ravvivare la mola in caso di necessità.
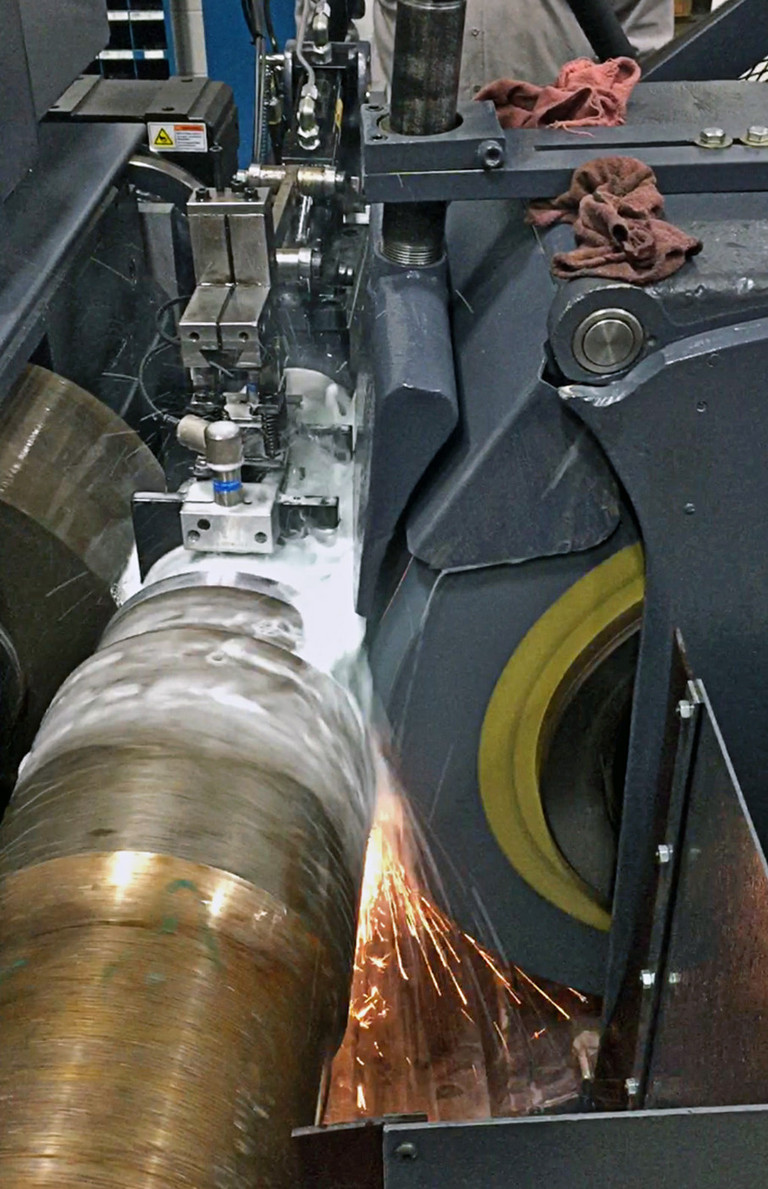
Questa è la seconda volta che APeC ha migliorato le prestazioni di queste rettificatrici con sistemi di controllo basati su kernel CNC NUM. Le macchine originali sono state azionate idraulicamente e dotate di sistemi di finitura di tipo tracciante. Nella metà del 1990, APeC ha eseguito un aggiornamento meccanico ed elettrico completo su ogni macchina che includeva il retrofit di un moderno sistema di CNC e strumenti di misurazione continua. In questa occasione, la società ha basato gli aggiornamenti su Power 1060 di NUM che al momento era considerato uno dei sistemi CNC più flessibili e facili da usare presenti sul mercato.
Dopo un funzionamento a tempo pieno per altri 20 anni in un ambiente di produzione intenso, le macchine erano pronte per un altro aggiornamento meccanico ed elettrico. APeC aveva supportato le macchine e lavorato a stretto contatto con i propri operatori in tutto questo periodo durante il quale aveva sviluppato anche una serie di idee per rendere le macchine ancora più facili da usare e più produttive. Il programma di aggiornamento ha offerto l’occasione ideale per mettere in pratica molte di queste idee.
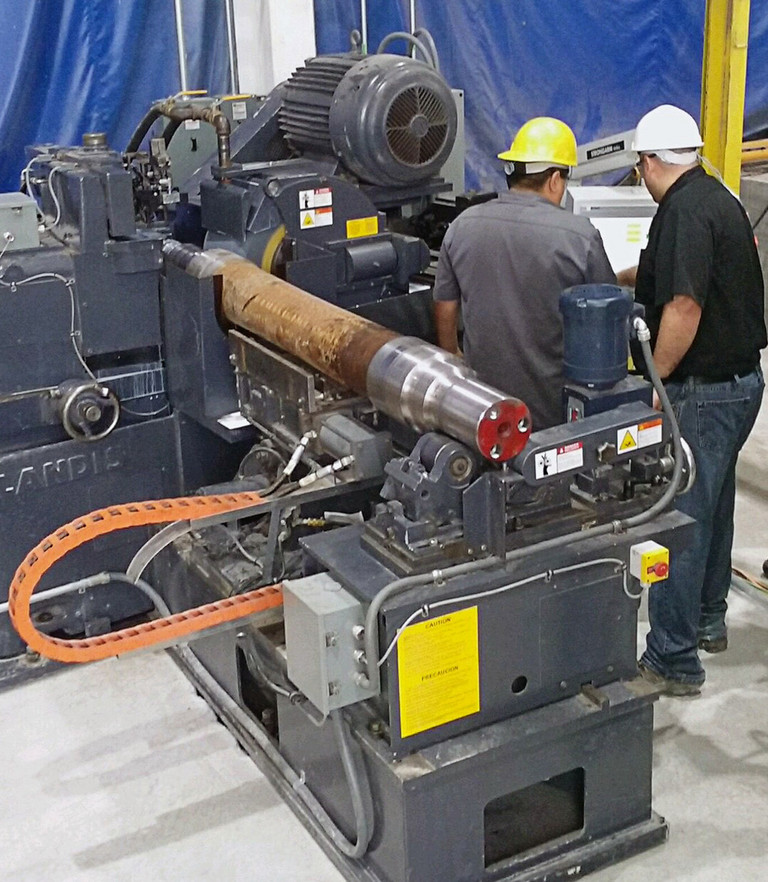
Per velocizzare l’aggiornamento della macchina e ridurre al minimo l’impatto sui programmi di produzione dei propri clienti, APeC ha gestito un partenariato per lo sviluppo a tre vie. Tutti i principali aspetti di ri-progettazione meccanica, idraulica, lubrificazione e gli aspetti geometrici di ricostruzione del progetto sono stati affidati a specialisti di EURO Machinery, Inc., una società con 45 anni di esperienza nella ristrutturazione e la modernizzazione di macchine utensili per il taglio dei metalli ad alto valore. Dal punto di vista del controllo, APeC ha collaborato con NUM Stati Uniti per sviluppare un’interfaccia uomo-macchina (HMI, Human Machine Interface) unica ed intuitiva. Ciò consente agli operatori di imparare a usare le macchine molto facilmente e rapidamente, anche se non hanno familiarità con questi tipi di rettificatrici. I vantaggi per il cliente sono la soddisfazione migliorata dei lavoratori, meno necessità di formazione e una maggiore produttività della macchina.
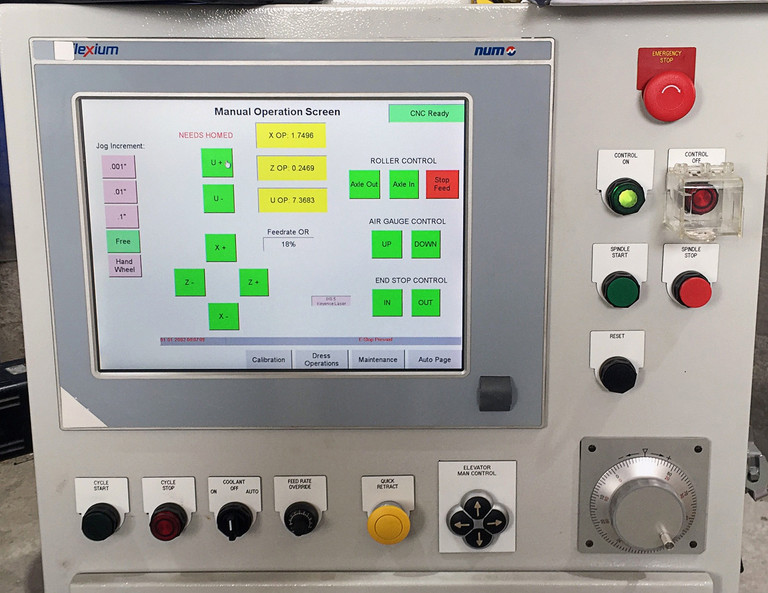
Secondo Dave DeCoursey of APeC, “Un obiettivo fondamentale del progetto era semplificare il funzionamento della macchina il più possibile. La piattaforma aperta Flexium CNC di NUM fornisce la flessibilità di controllo e i servizi di personalizzazione HMI necessari per sviluppare i singoli schermi basati sui task. L’interfaccia utente è quindi ora molto più ergonomica. La maggior parte delle operazioni, come ad esempio i calcoli offset, la calibrazione, la finitura e l’avvio automatico del ciclo di rettifica, vengono ora eseguite utilizzando singoli pulsanti virtuali che vengono visualizzati solo al momento opportuno.”
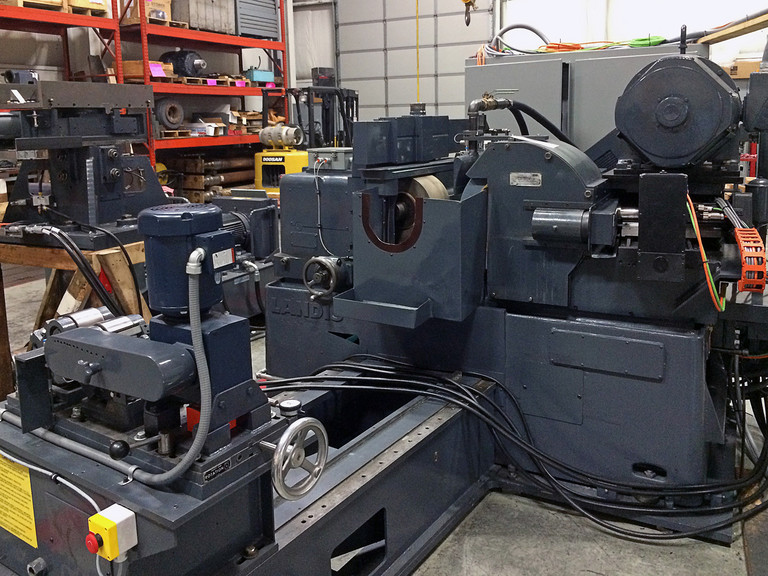
Ogni aggiornamento macchina utilizza diversi prodotti NUM, tra cui il kernel CNC, il pannello operatore sensibile al tocco, servoazionamenti e motori. Il sistema Flexium CNC utilizza comunicazioni EtherCat I/O che consentono ad APeC di semplificare l’implementazione di un’architettura di controllo avanzato della profondità di immersione. La strumentazione di misura continua precedentemente utilizzata per questo aspetto del funzionamento della macchina è stata sostituita da un encoder lineare che facilita il controllo veloce e preciso della profondità oltre a fornire un feedback in tempo reale per l’operatore durante il ciclo di rettifica. La schermata di controllo principale presenta due grandi quadranti in stile analogico, supportati da display digitali che derivano i dati di ingresso da sonde di misurazione separati situate lungo la lunghezza del perno dell’asse, consentendo all’operatore di monitorare molto facilmente la tolleranza conicità.
Il software HMI specifico per client e per applicazioni che APEC ha sviluppato per l’aggiornamento della rettificatrice è basato sui task. Utilizza schermi singoli su misura per l’applicazione, con funzioni sensibili al contesto chiare che aiutano a prevenire l’errore umano. Utilizzando i servizi Extended NCK Access (ENA) del controller Flexium CNC, ogni visualizzazione personalizzata basata su PLC può controllare e monitorare direttamente le funzioni CNC. Questa forma di approccio di controllo è particolarmente utile per la funzionalità automatizzata di tipo teach, come ad esempio guidare un operatore nell’avvio macchina e la preparazione dei cicli automatici.
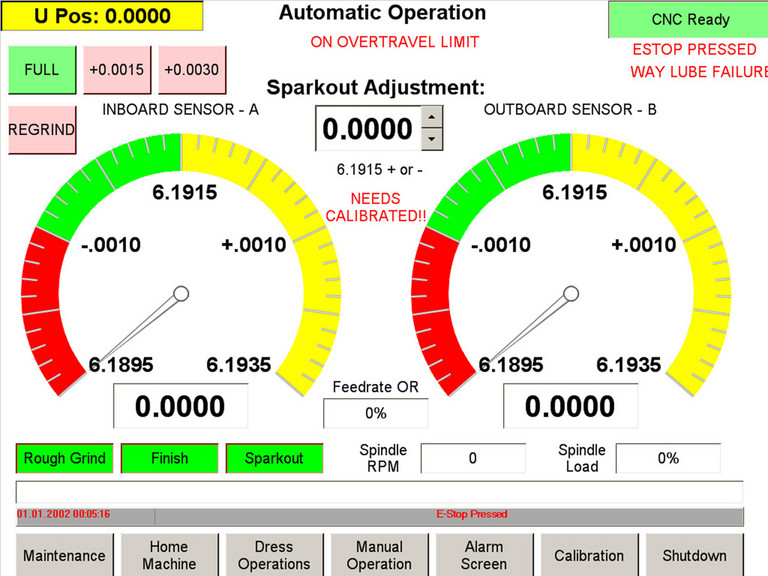
Ad esempio, la schermata di avvio visualizza inizialmente solo lo stato del sistema CNC e un unico pulsante ‘Shutdown’ (Spegnimento). Non appena il sistema CNC indica che è pronto, la schermata iniziale visualizza due pulsanti aggiuntivi: Home Screen (Schermata principale) e Manual Operation (Funzionamento manuale). Quando l’operatore tocca un pulsante visualizzato e provoca un cambiamento di schermo, il software modifica automaticamente la modalità CNC e seleziona il programma del pezzo corrispondente, se applicabile. Limitando le opzioni disponibili per l’operatore soltanto a quelle appropriate al momento, il software consente di garantire un uso coerente ed efficace della macchina.
Un altro grande vantaggio di questo tipo di approccio di controllo, con accesso esteso al NCK, è che può essere utilizzato per aiutare l’operatore negli offset dello strumento e gli adeguamenti delle dimensioni del programma del pezzo. Quando la ruota di rettifica o l’utensile di finitura viene sostituito, l’operatore può posizionare manualmente l’utensile sulla superficie desiderata della ruota, accedere a una schermata protetta da password e poi semplicemente premere un pulsante. Gli offset vengono calcolati e spinti automaticamente nel programma di finitura, utilizzando il servizio ENA. Questa stessa funzione consente all’operatore di modificare le dimensioni di finitura e i setpoint delle scintille regolando semplicemente un valore alto o basso. Questi vengono poi inseriti nel corrispondente programma del pezzo.
Steven Schilling, General Manager di NUM Corporation a Naperville, Illinois, dice: “L’architettura aperta e la funzionalità avanzata dei sistemi Flexium CNC consentono alle aziende di ingegneria di implementare sistemi di controllo macchina innovativi per retrofit o nuovi progetti di macchine utensili. In questo caso, APeC e Euro Machinery Specialists, con il supporto di NUM, hanno creato un retrofit CNC che aggiunge un valore significativo ai servizi di produzione esistenti del cliente.”
(Ottobre 2015)