Steinemann and NUM Collaboration: Swiss Precision par Excellence
In the increasingly globalized wood panel industry, Steinemann Technology AG is represented all over the world. A dense network of subsidiaries and representatives creates great market and customer proximity. When it comes to innovations, Steinemann relies on Swiss precision and reliability, which have characterized every Steinemann sanding system for more than half a century. The cooperation between Steinemann and NUM has a very long tradition, which has been increasingly consolidated and proven over time. That is why Steinemann once again relied on a complete CNC package from NUM for a retrofit of the Geminis GE-870S groove milling machine.
From textile machines to wide belt sanding machines for the panel industry
Founded in 1917, the family-owned Steinemann company has evolved from a manufacturer of textile machines to the world’s leading supplier of wide belt sanding machines and sanding systems for the wood-based panel industry. The company clearly differentiates itself from its competitors in the market through the outstanding quality of first-class surfaces. With modularly expandable products and services, Steinemann offers comprehensive solutions for surface finishing.
Steinemann pursues a clear strategy: maximizing customer benefits and securing decisive competitive advantages through “Total Surface Quality“. The company is headquartered in St. Gallen, Switzerland, and employs around 90 people. The St. Gallen textile tradition is reflected in the origins of the company; in the early days, it manufactured textile machines and then in 1960, it began manufacturing wide belt sanding machines for the wood panel industry.
The know-how goes far beyond development and production. Customers benefit from seamless services, in-depth process knowledge, and directly available spare parts and consumables. Thanks to this depth of service, Steinemann increases the quality, safety and efficiency of its customers. In addition to the headquarters in Switzerland, there are two subsidiaries. These are located in Malaysia and China to cover the growing Asian market with Swiss precision. In addition, there are country representatives in 42 other countries, and Steinemann employs a total of 130 people worldwide.
Fully integrated and automated grinding process
Steinemann is a full-range supplier of wide belt sanding machines for surface finishing. It focuses on the continuous development of machines and abrasives and supports customers in the integration of the sanding line as well as the optimization of the entire sanding process. In addition, there are further competences such as: development of abrasive systems, worldwide customer service, spare parts and consumables, and innovative automation technology.
The central elements for optimal sanding results are, among others, the rollers of the wide belt sanding machine. All rollers for all generations of machines are produced at the headquarters, including those for the company’s latest satos TSQ machines. The roller production process is very demanding due to the size and weight of the rollers. For example, rollers weighing 1.5 tons are balanced with an accuracy of less than 5 grams to avoid resonance of the grinding machine. The rollers are manufactured with very small tolerances. The finished rollers serve as a carrier for the sanding belts. MDF, particleboard and plywood up to a width of 3.2 meters are processed. Depending on customer requirements, the machine is composed of different numbers of “heads“. Highest precision is a central requirement at Steinemann and it is here that NUM makes a significant contribution.
Cooperation for over 20 years
Let’s go back in history about 20 years. As a progressive and innovative company, Steinemann decided to purchase a complete CNC system from NUM in 2000. The starting point was the conversion of a Geminis GE-870S lathe into a groove milling machine. The project involved a new control cabinet, new motors, a NUM 1040 CNC system and NUM MDLA drives.
Due to the aging control system and material fatigue of the electric cables caused by oil and contamination, in 2021 Steinemann decided to modernize the grooving machine in accordance with the latest technological requirements and safety regulations. This was of course also done with a view to avoiding possible future production downtime. For the new NUM CNC control, the company opted for a Flexium+ 6 with safety functions, NUMDrive X servo drives, and BPG motors with absolute measuring systems.
The wiring of the machine has been simplified and the use of the absolute measuring systems has eliminated referencing of the axes. The machining programs have been completely revised and parameterized so that the operator can create a new program in the shortest possible time. Data input is now done directly in the HMI (Human Machine Interface) on the corresponding variable pages.
During the modernization of the machine, it was also possible to optimize user-friendliness at the same time. This retrofit has led to a convincing added value of the groove milling machine. Operation has been significantly simplified, the setup time shortened, and process reliability increased. When you talk to the machine operators, you immediately gain an impression of how much they enjoy working on this machine.
It is also remarkable that this project could be realized by the same software developer, Mr. Konrad Näscher, Software Engineering NUM, who carried out the original retrofit 20 years ago. This long experience proved to be a great advantage in this retrofit. Mr. Näscher knew the machine characteristics and the programming very well and was involved in the project from the very beginning. Mr. Daniel Merkofer, Drums Department Manager at Steinemann, says: “The optimized user-friendliness leads to great satisfaction in operating the machine.”
The problem of re-entry has also been improved. Re-entry after a program abort has become much easier. The operator enters the approximate Z position of the groove, the control calculates the exact C position, moves to the Z-C position at rapid traverse, pierces the groove and finishes machining the groove. It is important that no groove marks are created during this process. Mr. Näscher says, “Experiencing the machine operators’ joy while working on the machine is very satisfying to a developer.”
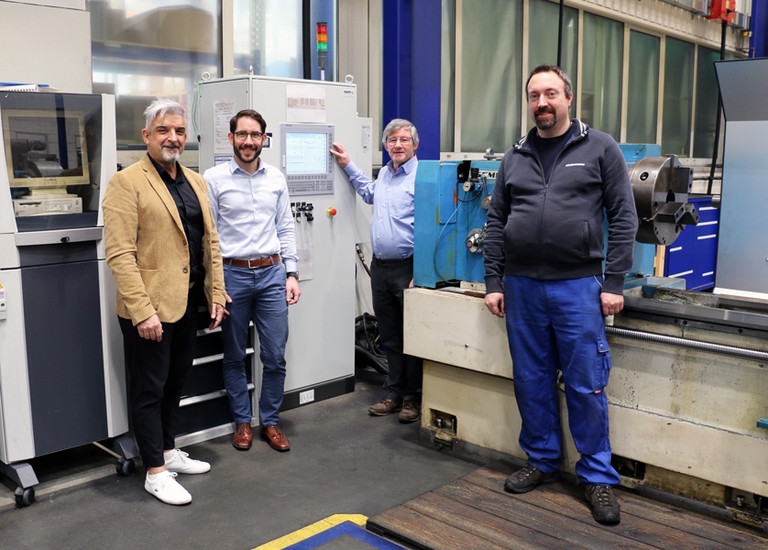
Minimal downtime during retrofit
Mr. Ilhan Hasdemir, Head of Quality Control/Warehouse/Production at Steinemann, adds: “From kick-off to commissioning, the retrofit went smoothly. Only a few fine adjustments were necessary during commissioning and the planned reserve time was not used. The machine downtime was kept as short as possible. The project was also a precision landing in terms of cost planning. From the quotation to the invoice, everything just fit and no additional budget was needed here either.” The entire planning process up to commissioning was uncomplicated and professional implementation was guaranteed on both sides. Mr. Hasdemir further enthuses: “The support from NUM was highly professional. You could always feel that there was a lot of passion, know-how and interest in the implementation of the retrofit.”
(September 2022)