Collaboration Steinemann et NUM : la précision suisse par excellence
Dans l’industrie de plus en plus mondialisée des panneaux de bois, Steinemann Technology AG est présente dans le monde entier. Un réseau dense de succursales et de représentations lui permet d’être très proche du marché et de ses clients. En matière d’innovation, Steinemann Technology AG mise sur la précision et la fiabilité suisses qui caractérisent chaque système de ponçage Steinemann depuis plus d’un demi-siècle. La collaboration entre Steinemann Technology AG et NUM AG présente une très longue tradition qui s’est renforcée et a fait ses preuves au fil du temps. C’est pourquoi Steinemann Technology AG a de nouveau misé sur le package complet de NUM pour un rétrofit de la fraiseuse de rainures Geminis GE-870S.
De la fabrication de machines textiles aux ponceuses à large bande pour l’industrie des panneaux à base de bois
L’entreprise familiale Steinemann Technology AG, fondée en 1917, est passée du statut de fabricant de machines textiles à celui de premier fournisseur mondial de ponceuses à larges bandes et de systèmes de ponçage pour l’industrie des panneaux en bois. L’entreprise se distingue clairement de ses concurrents sur le marché par la qualité exceptionnelle de ses surfaces de première classe. Grâce à ses produits et services modulaires et extensibles, Steinemann Technology AG propose des solutions complètes pour le traitement des surfaces.
Steinemann Technology AG poursuit une stratégie claire : maximiser les avantages pour le client et assurer des avantages concurrentiels décisifs grâce à la « qualité totale des surfaces ». L’entreprise a son siège à Saint-Gall, en Suisse, et emploie environ 90 personnes. La tradition textile saint-galloise se reflète dans les origines de l’entreprise familiale. À ses débuts, l’entreprise fabriquait des machines textiles. En 1960, Steinemann Technology AG a commencé à fabriquer des ponceuses à large bande pour l’industrie des panneaux de bois.
Le savoir-faire va bien au-delà du développement et de la fabrication. Les clients bénéficient de prestations de service sans faille, de connaissances approfondies des processus ainsi que de pièces de rechange et de consommables directement disponibles. Grâce à cette profondeur de prestations, Steinemann Technology AG améliore la qualité, la sécurité et l’efficacité de ses clients. Outre le siège principal en Suisse, il existe deux succursales. Celles-ci se trouvent en Malaisie et en Chine afin de couvrir le marché asiatique en pleine croissance avec la précision suisse. De plus, il existe des représentations nationales dans 42 autres pays, ce qui fait que Steinemann emploie au total 130 personnes dans le monde entier.
Processus de ponçage entièrement intégré et automatisé
Steinemann Technology AG est un fournisseur complet de ponceuses à larges bandes pour le traitement des surfaces. Elle se concentre sur le développement continu des machines et des abrasifs et supporte ses clients dans l’intégration de la ligne de ponçage ainsi que dans l’optimisation de l’ensemble du processus de ponçage. A cela s’ajoutent d’autres compétences telles que : Le développement de systèmes d’abrasifs, un service client présent dans le monde entier, des pièces de rechange et des consommables ainsi qu’une technique d’automatisation innovante.
Les rouleaux de la ponceuse à larges bandes constituent, entre autres, l’élément central pour des résultats de ponçage optimaux. Tous les rouleaux de toutes les générations sont produits au siège principal, principalement pour la dernière génération de machines satos TSQ. Le processus de fabrication des rouleaux est très exigeant en raison de leur taille et de leur poids. Ainsi, les rouleaux de 1,5 tonne sont équilibrés avec une précision de moins de 5 grammes afin d’éviter les résonances de la rectifieuse. Les cylindres sont fabriqués avec des tolérances minimes. Les rouleaux finis servent de support aux bandes abrasives. Les panneaux MDF, d’aggloméré et de contreplaqué jusqu’à une largeur de 3,2 mètres sont usinés. En fonction des exigences du client, la machine est composée d’un nombre variable de «têtes». La plus haute précision est une exigence centrale chez Steinemann Technology AG et NUM y apporte une contribution essentielle.
Une collaboration de plus de 20 ans
Revenons une vingtaine d’années en arrière dans l’histoire. En tant qu’entreprise progressiste et innovante, Steinemann Technology AG a décidé en 2000 d’acquérir un système CNC complet de NUM. Le point de départ a été la transformation d’un tour Geminis GE-870S en une fraiseuse de rainures. L’armoire électrique les moteurs jusqu’à la commande CNC NUM 1040 avec entraînements MDLA ont été complétés.
En raison de la commande vieillissante et de la fatigue des matériaux des câbles électriques due à l’huile et à l’encrassement, Steinemann Technology AG a décidé en 2021 de moderniser la fraiseuse de rainures selon les dernières exigences technologiques et les règles de sécurité. Cette décision a bien entendu été prise dans le but d’éviter d’éventuelles futures pertes de production. Pour la nouvelle commande CNC NUM, l’entreprise a opté pour une Flexium+ 6 avec Safety, NUMDrive X avec moteurs BPG équipés de systèmes de mesure absolus.
Le câblage de la machine a été simplifié et l’utilisation de systèmes de mesure absolus a permis d’éliminer le référencement des axes. Les programmes d’usinage ont été entièrement revus et paramétrés, ce qui permet à l’opérateur de créer un nouveau programme en très peu de temps. La saisie des données se fait désormais directement dans l’interface homme-machine (IHM) sur les pages variables correspondantes.
Lors de la modernisation de la machine, la convivialité a également été optimisée. Ce rétrofit a permis d’apporter une plus-value convaincante à la fraiseuse de rainures. L’utilisation a été considérablement simplifiée, le temps de réglage a été réduit et la sécurité du processus a été augmentée. Lorsqu’on parle avec les opérateurs, on sent qu’ils prennent beaucoup de plaisir à travailler sur cette machine.
l est également remarquable que ce projet ait pu être réalisé par le même développeur de logiciels, Monsieur Konrad Näscher (Développement Logiciel NUM) qui avait déjà réalisé le premier rétrofit il y a 20 ans. Cette longue expérience s’est avérée être un grand avantage pour ce rétrofit. Monsieur Näscher connaissait très bien les caractéristiques de la machine et la programmation et a été impliqué dans le projet dès le début. Monsieur Daniel Merkofer, chef du département Drums de Steinemann Technology AG, déclare : « La convivialité optimisée entraîne une grande satisfaction lors de l’utilisation de la machine. »
Le problème de la réintégration a également été amélioré. La reprise après une interruption de programme est devenue beaucoup plus simple. L’opérateur saisit la position Z approximative de la rainure, la commande calcule la position C exacte, se déplace en avance rapide jusqu’à la position Z-C, pique dans la rainure et termine l’usinage de la rainure. Il est important qu’aucune trace de piqûre n’apparaisse lors de ce processus. M. Näscher déclare : « Voir le plaisir des opérateurs travaillant sur la machine est le plus grand remerciement que l’on puisse adresser à un développeur. »
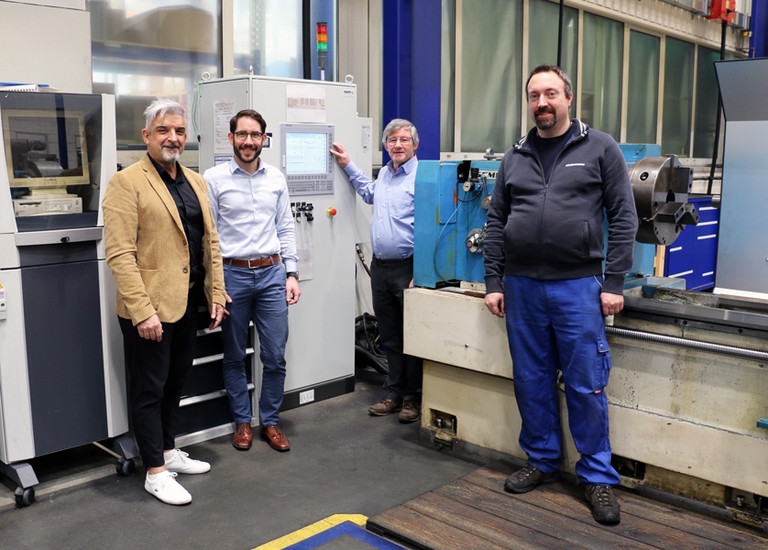
Temps d’arrêt minimal pendant le retrofit
Monsieur Ilhan Hasdemir, Head of Quality Control/Warehouse/Production Steinemann Technology AG, ajoute : « Du kick-off à la mise en service, le rétrofit s’est déroulé sans problème. Lors de la mise en service, seuls quelques réglages fins ont été nécessaires et le temps de réserve prévu n’a pas été utilisé. Le temps d’arrêt de la machine a été aussi court que possible. Le projet a également été un atterrissage de précision en ce qui concerne la planification des coûts. De l’offre à la facture, tout a été parfait et, comme je l’ai dit, aucun budget supplémentaire n’a été nécessaire. » L’ensemble du processus de planification jusqu’à la mise en service a été simple et la mise en œuvre professionnelle a été garantie des deux côtés. M. Hasdemir poursuit avec enthousiasme : « L’assistance de NUM a été des plus professionnelles. On a toujours senti qu’il y avait beaucoup de passion, de savoir-faire et d’intérêt pour la mise en œuvre du rétrofit.
(Septembre 2022)