Innovative neue Serie von Spiralbohrern dank fortschrittlicher CNC-Simulationssoftware
Mit Hilfe von CNC-Mehrachsenschleifmaschinen und der 3D-Simulations- und Steuersoftware NUMROTOplus von NUM fertigt das Unternehmen Miller Präzisionswerkzeuge GmbH eine neue Serie von VHM-Hochleistungsbohrern der Marke MAPAL. Bei diesen neuen Bohrern finden komplexe, optimierte Profile Anwendung, um die Bearbeitungszeiten zu verkürzen.
Mit der NUMROTOplus-Software ist Miller Präzisionswerkzeuge in der Lage, den für die Fertigung der neuen Bohrer erforderlichen komplexen Bearbeitungsprozess dreidimensional zu visualisieren und zu optimieren, bevor die neue Bohrerserie in die Massenproduktion geht. „Die NUMROTO-Funktionen waren bei der Entwicklung unserer neuesten MAPAL-Bohrer sehr hilfreich, und wir haben die 3D-Simulationsmöglichkeit der NUMROTOplus-Software, einschließlich der Verfahren zur Kollisionsüberwachung, umfassend genutzt, um unseren Fertigungsprozess zu optimieren“, berichtet Ulrich Krenzer, Technischer Leiter von Miller Präzisionswerkzeuge.
„Wir arbeiten bereits seit mehreren Jahren mit der CNC-Software von NUM und sind jetzt dabei, sie für alle unsere Maschinen anzuwenden. Durch die effiziente Standardisierung dieses Softwarepakets mit einer konsistenten Bedienoberfläche können wir die Schulungskosten für unser Personal reduzieren, die Produktivität maximieren und gleichzeitig die Produktqualität, für die wir bekannt sind, aufrechterhalten.“
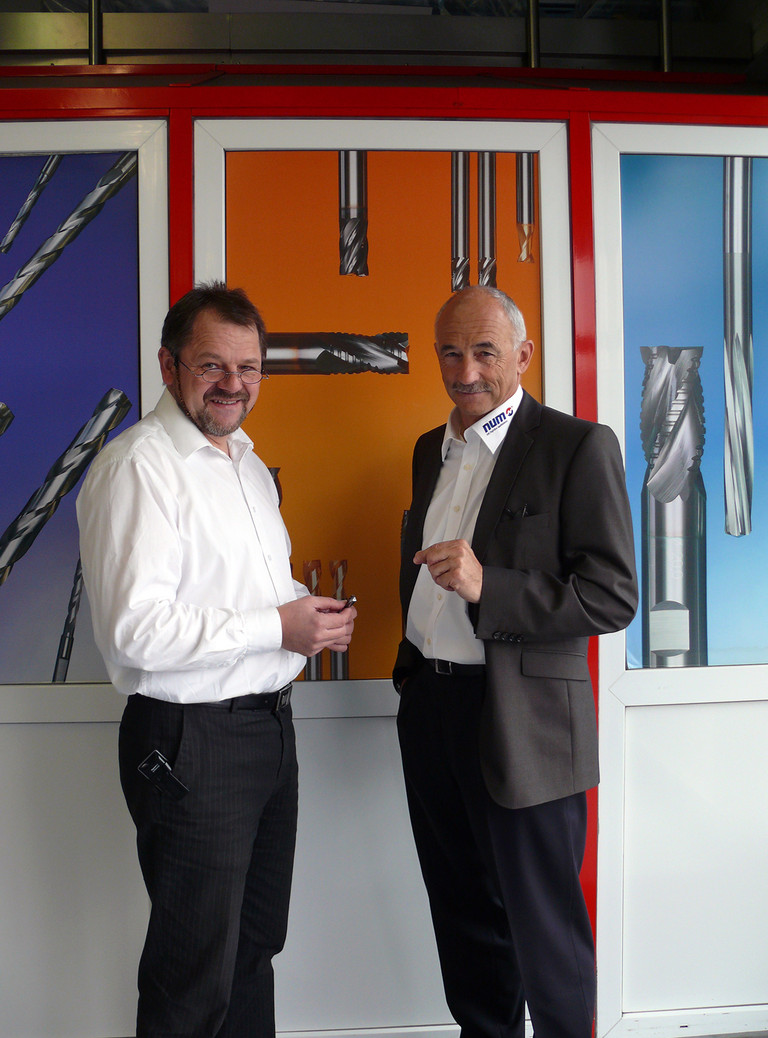
Um den Bedarf decken zu können, hat Miller Präzisionswerkzeuge kürzlich die Größe seines Fertigungsbetriebs mit angeschlossener F/E-Einrichtung in Altenstadt verdoppelt. Im November 2008 wurde eine neue Fertigungsanlage mit einer Größe von 7000 m2 in Betrieb genommen. Diese Anlage umfasst mehr als 40 CNC-Schleifmaschinen, die mit der NUMROTOplus-Software ausgerüstet sind und 365 Tage im Jahr im Dreischichtbetrieb arbeiten. Damit ist dies die weltweit modernste Anlage zur Fertigung von VHM-Werkzeugen und -Bohrern. Man geht allgemein davon aus, dass die Bohrvorgänge über 30 Prozent der produktiven Maschinenzeit ausmachen. Dazu gehören in der Regel das Vorbohren und Zentrieren, das Reiben, Senken, Aufbohren, Fasen und Gewindeschneiden. Durch die Kombination einiger dieser Vorgänge in einem einzigen Schritt lässt sich die Bearbeitungszeit erheblich verkürzen – dies ist aber nur möglich, wenn die Bohrwerkzeuge für die jeweilige Aufgabe optimierte Profilgeometrien aufweisen. Wichtige Faktoren sind die Spanabnahme, die Wärmeableitung und die Werkzeugstabilität.
Der neue MAPAL „Mega Speed Drill“ ist für das Hochgeschwindigkeitsbohren von Stahl und Eisen ausgelegt. Er verfügt über eine asymmetrische Spitze mit verstärkten Schneidkanten. Die drei Freiflächen sind so gestaltet, dass der Bohrer die Bohrungen etwas erweitert und so die Reibung zwischen den Querscheiden und dem Werkstück minimiert. Dank dieser Geometrie ist der Bohrer relativ unempfindlich gegen hohe Schneidkantentemperaturen und Eckenverschleiß. Die speziell geformte, polierte Nut gewährleistet die ungehinderte Spanabnahme. Der Bohrer lässt sich bei der Stahlbearbeitung mit einer sehr hohen Schneidgeschwindigkeit (ca. 200 m/min) betreiben, wodurch die Bearbeitungszeit im Vergleich zu herkömmlichen Produkten um bis zu 70 % reduziert werden kann.
Wenn das Werkzeug z. B. zum Hochleistungsbohren von vergütetem Stahl 42CrMo4 verwendet wird, liegt die typische Lebensdauer bei 60 bis 70 m, wodurch eine Senkung der Fertigungskosten je Bohrung um bis zu 50 % möglich wird.Darüber hinaus hat Miller Präzisionswerkzeuge gerade einen Spiralbohrer entwickelt, der eine Bohrung mit einer ebenen Grundfläche von 180 Grad erzeugt. Dazu wären normalerweise zwei Bearbeitungsvorgänge erforderlich; im ersten würde die Bohrung mit der erforderlichen Tiefe hergestellt werden und im zweiten das Senken erfolgen. Durch ein spezielles Spitzenprofil werden diese beiden Vorgänge beim neuen „Mega Drill 180“ effizient in einem Bearbeitungszyklus kombiniert. Die Bohrer werden mit einer S-förmigen Ausspitzung geschliffen, was eine gute Spankontrolle gewährleistet und eine profilierte konkave Flanke erzeugt, die zu einer ebenen Grundfläche der Bohrung führt. Das Werkzeug ist auch zum Vorbohren an geneigten Flächen geeignet. Durch die flache Spitze werden hierbei die Radialkräfte im Vergleich zu herkömmlichen 140-Grad-Bohrer-spitzen reduziert.
(Oktober 2009)