CNC 高精度磨削中心
提及用于生产直径小至 0.02 mm 或长度达 450 mm 的螺旋钻的机床时,TTB (SAACKE Group) 绝对是业内主要创新者之一。该公司制造高精度刀具磨床,配备最新的 NUM CNC 控制系统,可提供刀具磨床应用的客户专用技术,范围包括碳化物、HSS 和其他特殊材料。TTB 和 NUM 之间极为高效的协作如今已步入第 10 个年头,双方在开发新产品方面持续进行广泛的技术交流。
在 2012 年 GrindTec 博览会上,TTB 发布了其磨削技术的最新创新产品 —— TG10 高精度磨削中心。该最新一代专用机床采用独有的垂直轴配置,最小化实体空间要求,同时提高了生产速度。机床线性轴采用行星驱动系统,以最大化可靠性;出于相同原因,这一技术也应用在航空航天工程领域。结合轴动力学对称排列,实现了比常规机床快 3 倍的进给运动,同时也助力于 TG10 实现极其紧凑的设计。
机床由 NUM Flexium CNC 系统和 NUMROTOplus 刀具磨床软件控制,提供直接且极为高效的刀具设计和制造途径。
全新 TG10 遵从与 TTB 的知名 TGC 和 Evolution 磨床相同的高质量标准制造而成,标志着该公司在成本控制工程方面迈出了第一步。当前变幻莫测的市场需求使机床所形成的的生产率、适应性和效率更高,而价格却尽可能低廉,但不会影响质量,TTB 研发 TG10,正是对这一市场趋势的直接响应。以较低购置成本打造高质量和精度机床这一设计目标已经完美实现,这也让 TTB 在这一细分市场获得了压倒性优势。令 NUM 感到十分欣慰的是,NUM 对新机床的开发提供了帮助和支持,同时以其使命为荣:“NUM CNC 解决方案助力于机床制造商获得竞争优势”。
TG10 的全新动力学将精确控制移动引入刀具磨床工艺。机床的创新型垂直轴架构由 TTB 开发,充分利用 NUM 最新一代轴驱动器的优异性能,通过最快的进给率和最短的过渡路径提高生产率。极其紧凑的设计特性确保了极高的稳定性和刚性;机床仅需用户在生产设施中提供极小的空间,安装极为简便,同时有效降低了成本。
TG10 全新砂轮更换装置进一步加快了生产周期。旋转装置明显减少了主轴更换时间,标准砂轮更换装置可升级为带最多4 个夹紧装置。自动上料装置可承载最多800 个工件,直径 16 mm,最大长度150 mm,便于进行不间断的批量生产;上料装置有不同版本,可根据用户需求提供。
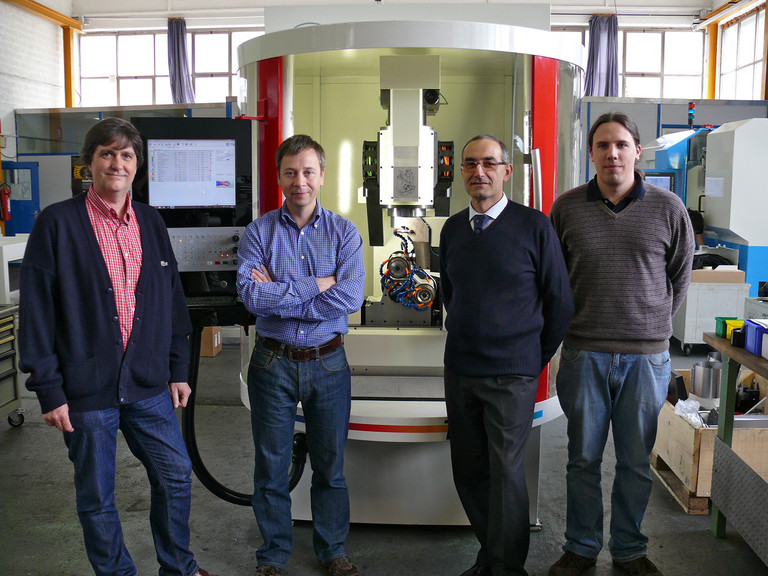
NUMROTOplus 应用软件、先进的 CNC 控制和创新型动力学的组合将无与伦比的适应性引入加工工艺。TG10 性能显著超出传统刀具磨床,确保机床制造商以可靠、低成本的方式加快生产。对于大批量生产和小批量生产,机床均可适用,即使是全新开发的定制刀具也可轻松加工,同时确保成本低廉。
(九月 2012)