Partnership for Target to Cost Design
The Michelin Man is one of the most recognized icons in the world. Anyplace, where tires are found, the majority of people will know how to associate Michelin and the quality of its products with ‘Bibendum’. On the other hand, the fact that Michelin has trusted NUM for several decades is much less well known.
Quality is reflected in the details and Michelins knows this - by displaying the same care for quality in the rubber and structure to the extensive details on the sidewall of the tires. This goes so far as to make it feel like a ‘velvet touch’ on some tires.
The tires are baked inside a mold. This one is made of several adjacent elements for the tread and two toric-looking flanks for the sidewalls. It is the engraving of these two pieces that interests us today.
Even though the tools are only a few millimeters in diameter, the quality of the engraving and the machined material require rigorous design, high rigidity and efficient control. The initial machine, of purely Michelin design, was already controlled by a NUM 1060 control system. Over the years, various improvements have been made. For the current version (CN5S) Michelin has reviewed the design in partnership with the company RGI France located in St Cere in the Mecanic Valley. This 100% French-owned company produces both standard machines and machines adapted to the specific needs of its customers. RGI France succeeds RGI, which had already established a long and fruitful cooperation with Michelin for retrofits or supplies of machines used to produce electrodes or inserts for snow tires. The study was carried out with a view to Design to Cost, which made it possible to optimize cost while further improving performance. NUM was of course involved in this process and the system quickly proved to be the right solution to manage the whole process. This study also included a comparative section with a standard machine and it quickly turned out that the solution chosen was the most efficient.
The five axes of the machine, capable of acceleration up to 5 m/s², are driven by four conventional motors plus one torque motor, all controlled by NUMDrive X drives equipped with SAMX safety modules; a 40,000 rpm electro spindle completes the assembly. In addition to the security they provide, these SAMX modules combined with the NUMSafe functionality will further improve production performance since it will be possible, for example, to perform operations with the protection enclosure being open, without having to switch off the power. The PLC is managed by a Box PC system and a second PC on the machine manages Michelin’s own machining management and supervision operations. A 22” portrait screen simultaneously displays this Michelin HMI and the NUM HMI with pages specific to RGI France.
The choice to have NUM be the supplier of the automation for this machine was a simple one. It should be noted that more than twenty identical machines exist from the USA to Thailand. The reliability of the systems and the quality of the support have never been lacking; moreover, as Mr. Boët, Prototypes Project Manager at Michelin, pointed out, “ease of use is appreciated as well as the compatibility of the part programs between successive versions”.
This is of course not the only reason for this partnership with NUM. Both RGI France and Michelin appreciate the proximity and quality of the relationships that make it possible to make the best use of Flexium+’s own functions. Mr. Lachat, Director of RGI France, said on this occasion that he had never encountered a challenge that the various NUM equipment failed to solve. “This latest evolution of the Flexium+ system has made it possible to implement an advanced lubrication function that will reduce environmental pollution while improving the service life of guides and bearings. We also note the quality of the drives and an excellent support from NUM for optimizing performance and eliminating parasitic resonances, which is another point for achieving a higher productivity.” Finally, in order to maintain this performance throughout the life of the machine, a performance monitoring function during this life cycle, described elsewhere in this issue of NUMinformation, will be implemented to detect potential mechanical problems before they have any adverse impact.
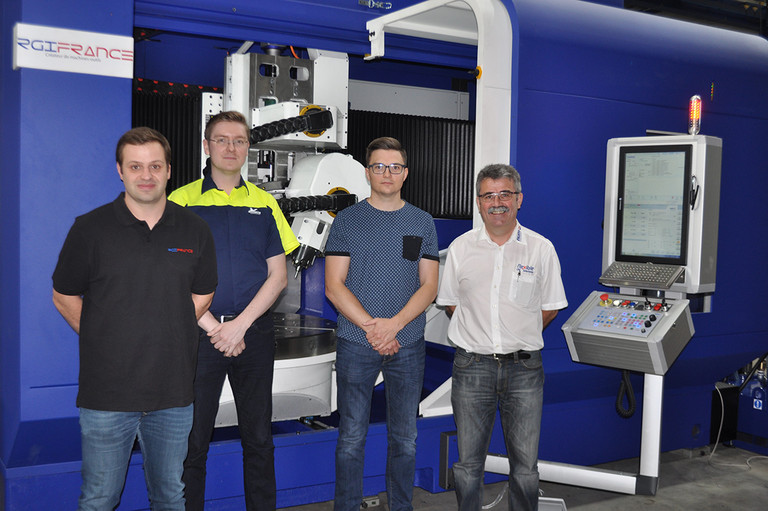
This example of partnership between the customer, the manufacturer and NUM is not unique. It corresponds well to the company’s philosophy of providing everyone with the necessary tools to make the best of their specific advantages. Do not hesitate to talk to your correspondents, they will be very happy to assist you in this way.
(September 2019)