When Numerical Control Makes the Difference
Ten years ago, Faimond, a small Italian company renowned for its expertise in crafting machine tools for the goldsmithing industry, made a strategic decision to expand its horizons by venturing into the dental sector. They chose to partner with NUM to deliver a comprehensive solution centered around Flexium+ 68, while also receiving support for system customization and integration.
Precision is paramount in the production of dental prostheses and specialized components. Whether crafting parts from grade five titanium or chrome-cobalt alloys, absolute accuracy is non-negotiable. Once a prosthesis is fabricated, there’s no room for adjustments. Precision isn’t just recommended - it’s essential.
In light of these principles, the pivotal role of technology becomes apparent. Achieving the micrometric precision demanded by the dental sector requires highly sophisticated solutions, enabling the manufacturing of components with tight tolerances and exceptional quality, all starting from the technical drawings.
Situated in Arcugnano, on the outskirts of Vicenza, is the headquarters of Faimond - a small business founded almost fifty years ago in the goldsmithing sector by Gianluigi Dal Lago. Over the years, Faimond has adeptly adapted to changing landscapes, leading to the establishment of a dedicated division for dental machinery a decade ago. Today, this division accounts for about a third of the company’s revenue, showcasing Faimond’s ability to turn necessity into opportunity.
Entry into the dental sector
“A few years ago we decided to expand our outlet areas”, explained Andrea Dal Lago, at the helm of the company together with his brother Fabio, as well as head of sales. “And so we looked for a sector that - from a technological point of view - was akin to the goldsmithing sector, so that we could exploit our know-how as much as possible.”
In this scenario, Faimond’s engineering department conceived an initial machine tailored for both the goldsmith and dental sectors: a compact five-axis continuous milling center with three distinct configurations. Each configuration varies based on the workpiece gripping system it’s equipped with—namely, for ring machining, dental sector machining, and micro-machining. The dental configuration proved most successful, initially introduced as the XD180 and now in its third iteration as the XD182. Faimond also announced the upcoming XD183 version, boasting significant new features and a notable reduction in footprint.
“Our typical customers are the dental laboratory”, continued Andrea Dal Lago, “or user with classic milling center, specialized in the development of dental components. In fact, the XD182 is mainly used for machining metal and, in particular, grade 5 titanium and a chrome-cobalt alloy, both materials mainly used for the production of bars on which dental implants are then fixed, or the internal capsules on which zirconia tooth prostheses are mounted.”
Notably, the XD182’s versatility extends to processing zirconia itself if required, although the material’s extreme brittleness mandates dry treatment and subsequent heat strengthening.
A niche market
In the realm of dental milling, machines vary widely in complexity. While ninety percent are simple and small, primarily used for processing soft materials like zirconia, Faimond has strategically positioned itself in a niche market. Specializing in the construction of metalworking solutions requiring advanced technology, Faimond’s machines are designed to achieve unparalleled precision.
The decision to integrate NUM’s Flexium+ 68 - a highly flexible numerical control system - into the XD182 was deliberate.
“After several researches”, explained in fact Fabio Dal Lago, head of the technical department, “we identified Flexium+ 68 as the solution that best matched our idea of numerical control, both from a technological point of view and for its quality/price ratio.”
Technology collaboration
NUM provided Faimond with a tailored turnkey solution, along with comprehensive support for system customization and integration.
“We dealt with the development of the PLC software to manage machine automation”, explained Marco Battistotti, NUM Italia’s NTC manager, “but also with the customizations of the ‘human-machine interface, with the aim of simplifying the use of the system for the target audience it was intended for. On Faimond’s instructions, we thus built graphic pages that would highlight the operations essential for dental technicians to operate the machine. And finally, we interfaced with the software house that developed the CAD/CAM used by Faimond and integrated it into our control.”
The XD182, a standard machine with customizable features, incorporates the complete NUM Flexium+ 68 system, featuring BHX motors and MDLUX drives.
A collaboration in the making
“In recent years we are seeing the complication of a certain type of application”, added Fabio Dal Lago. “If before we were dealing with customers who had to perform fairly basic machining, more and more we are encountering operators with more complex requirements. This implies - on a practical level - having to elevate the machine’s performance, through the development of dedicated macros for specific controls on the part, and it is precisely thanks to the choice of relying on a flexible control such as Flexium+ 68 and a team of highly qualified professionals such as those NUM provides, that it is possible to carry out a certain type of customization, pandering - in this way - to the needs of the market.”
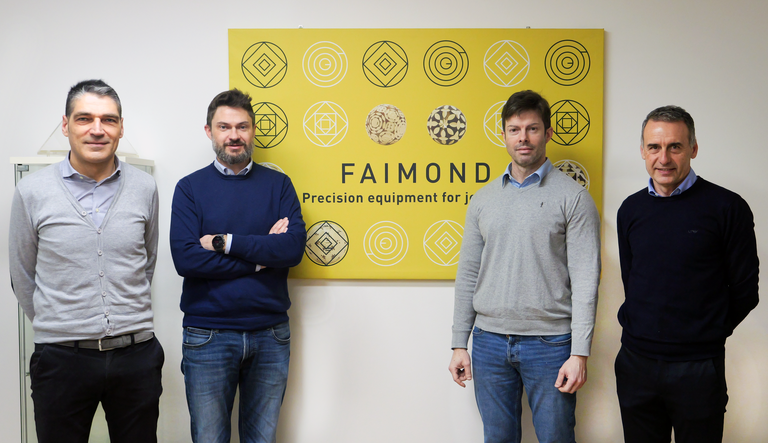
(September 2024)