High-precision 17-axis laser welding system for the automotive industry
In today’s market, in addition to efficient production, the automotive industry’s primary objectives are to reduce a vehicle’s fuel consumption and to improve passenger safety. In plain English, cars need to become lighter and safer at the same time. The laser welding system by Soutec combines these two main objectives by welding different plates of varying thickness and strength. Many of today’s cars contain body parts welded by Sutec. For complex, so-called “tailored blanks” and welding seams, ANDRITZ Soutec has enhanced its tried and tested “Soutrac” laser welding machine and equipped it with the latest technology and control system.
The heart of the machine is a 9-axis welding head. With it, even non-linear seams can be welded. The welding head is equipped with rotatable and height-adjustable cameras in front of and behind the welding nozzle, allowing for seam tracking and subsequent quality control, and guaranteeing a stable welding process that meets even the highest quality requirements. Gaps of <0.3 mm between plates are joined dynamically and in high quality during the welding process using filler wire (Soufil).
The welding system is controlled by a Flexium+ CNC system with safety functions and comprises two sections: the welding machine and the loading unit. It has a total of 17 axes. The X-axis of the welding machine is designed as a bridge with two motors, because the workbench with its magnetic fixation and material weighs 1.5 tons. It can be accelerated at 4 m/s2, allowing a start-up performance of 0 to 120 m/min within 1 second. The laser has an output of 6 kW and can weld seam plates of different strength and material. The weld speed is about 10-12 m/min.
The highly dynamic welding system is designed for accuracy and speed using high-precision mechanics and state-of-the-art CNC controls. By working closely together, ANDRITZ Soutec and NUM are helping the automotive industry to increase the flexibility, speed and accuracy of its production processes. Machine retooling is also quick and easy, simplifying product changeover. This minimizes production interruptions, thus further increasing system efficiency. By acquiring Soutec AG, based in Neftenbach, Switzerland, the Austrian group ANDRITZ was able to expand its product range for the metalworking industry in 2012 and strengthen its global presence. ANDRITZ Soutec is a provider of laser and roll seam resistance welding systems and has been working on developing CNC-controlled equipment in partnership with NUM for close to 30 years. Especially lightweight products, such as the body parts mentioned above, but also fuel tanks or exhaust system components, are produced with the Soutec welding systems at the end user's location.
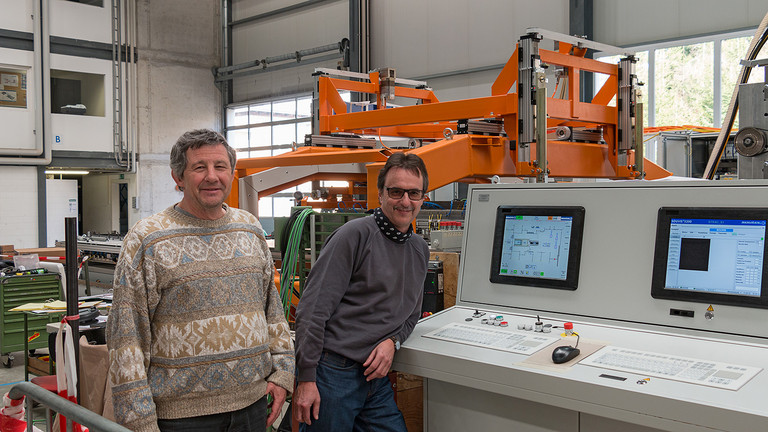
The ANDRITZ Soutec systems are designed to provide optimum support to automotive manufacturers in their continuous efforts to produce safe lightweight vehicle designs while ensuring a high level of profitability. ANDRITZ Soutec has therefore always worked closely with its customers to identify market needs as early as possible and to introduce innovative new products quickly. Case in point is the existing Soutrac system, which was enhanced and equipped to meet current demands.
For Soutec, merging with the ANDRITZ Group was a stroke of luck. The company seamlessly integrated into the Group’s structure while keeping its independence. Like Soutec, which started out as a small workshop over 60 years ago, the Group also started small: the foundation of a small iron foundry in Austria in 1852 marked its birth. In order to always be at the cutting edge of technology, ANDRITZ runs several research centers where products and processes are improved and developed to the highest standard. The Group focuses mainly on developing tailored technology solutions. This has always been the case for Soutec as well, collaborating closely with development partners such as NUM and the customer. In addition, the ANDRITZ Group focuses particularly on increased environmental protection, reducing the use of energy and resources in production as well as extending the service life of machines and systems.
(October 2015)