La mise à niveau avec les bons partenaires est payante
Un parc de machines bien équipé, régulièrement mis à jour avec les technologies les plus récentes, est l’épine dorsale de toute entreprise manufacturière. Ce « rajeunissement » s’opère généralement par l’acquisition de nouvelles machines, mais souvent aussi par des machines qui ont fait l’objet d’une remise à niveau complète. Ces machines entament ainsi une seconde vie, comme la rectifieuse cylindrique Ceres 330 de Karl Bruckner GmbH, qui a été modernisée par le spécialiste HDC Huttelmaier. Également à bord : NUM, fabricant de CNC et de logiciels.
Avec son innovation du centre rotatif, Karl Friedrich Bruckner a engendré des changements importants il y a plus de 100 ans. Aujourd’hui, la troisième génération de Karl Bruckner GmbH à Weinstadt, en Souabe, produit des machines de haute précision pour le tournage et la rectification, ainsi que de mandrins à facettes, d’entraînements à facettes et de fourreaux. Les produits sont fournis en tant qu’équipement d’origine à des fabricants de machines allemands renommés et à des clients du monde entier.
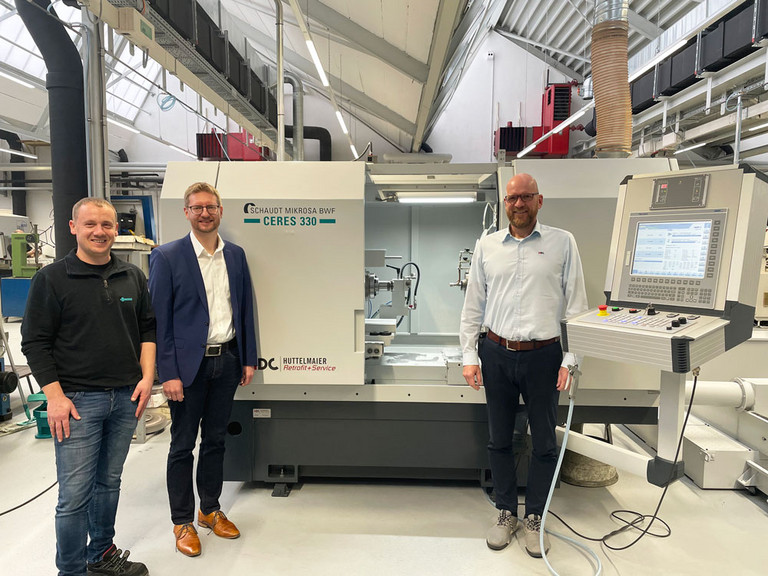
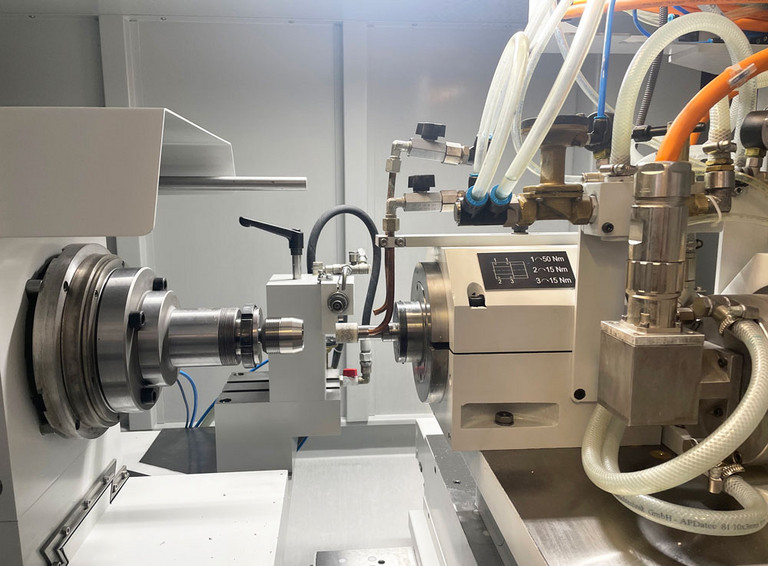
Le chargé de production Marc Sigle, responsable du bon déroulement de la production, est non seulement responsable des performances d’usinage des machines, mais il partage également la responsabilité de leur approvisionnement et de leur remplacement. Lorsqu’il est devenu difficile d’atteindre la précision requise avec la Ceres 330, Marc Sigle a exploré différentes options : « En termes de précision dimensionnelle et de stabilité du processus, la Ceres a été exemplaire au fil des ans. La machine a une conception relativement simple, mais elle était parfaitement adaptée à notre produit et a fonctionné comme une machine de production pure pendant toutes ces années, sans aucun problème », se souvient Marc Sigle, qui a lui-même travaillé sur la Ceres pendant plusieurs années et qui la connaît parfaitement. En fin de compte, cela s’est avéré avantageux à tous points de vue.
Au moment de l’achat, la Ceres 330 était l’une des dernières machines de sa série. L’ensemble du programme de machines du fabricant a alors été complètement arrêté. Comme il n’y avait plus de pièces de rechange ni de service après-vente, le responsable de production compétent qu’était Marc Sigle a pu se charger lui-même de nombreuses tâches au cours des dernières années. Selon Marc Sigle, le coût a joué un rôle important dans la décision de ne pas acheter une nouvelle machine, mais de moderniser la Ceres 330.
Par rapport à une machine neuve, une modernisation est environ 50 % moins chère. Toutefois, si l’on tient compte de tous les coûts, les économies sont encore plus importantes. La possibilité de continuer à utiliser les outils et les broches de rectification existants ne doit pas être sous-estimée. « Nous avions en stock un grand nombre d’outils appropriés et quatre broches de rectification de haute qualité d’une valeur de plusieurs 10 000 euros, que nous n’aurions pas pu continuer à utiliser si nous avions acheté une nouvelle machine. C’était un argument de poids en faveur d’un rétrofit », déclare Sigle.
Jörg Huttelmaier, propriétaire et directeur général de HDC Huttelmaier, spécialiste du rétrofit et constructeur de machines spéciales, que Marc Sigle avait connu lors d’un rétrofit partiel réussi, a présenté des arguments supplémentaires. Dans sa propre usine de construction de machines à Schorndorf-Weiler - à seulement 12 km de Bruckner - HDC Huttelmaier modernise actuellement des rectifieuses d’occasion pour les mettre à la pointe de la technologie, et ce, depuis la troisième génération de la famille. La vaste équipe de spécialistes Huttelmaier pour la maintenance, la modernisation et la révision des machines-outils et des équipements, et si nécessaire la sous-traitance qualifiée, garantissent une révision mécanique, géométrique et électrique complète et professionnelle pour chaque projet.
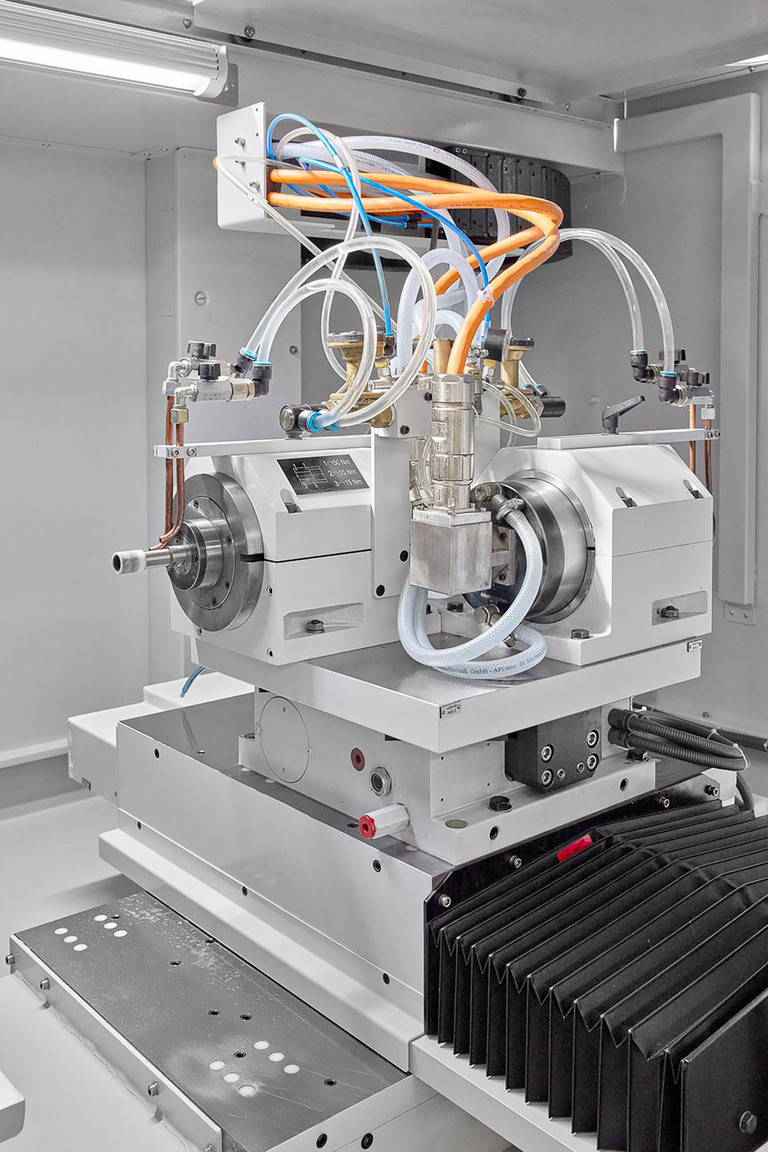
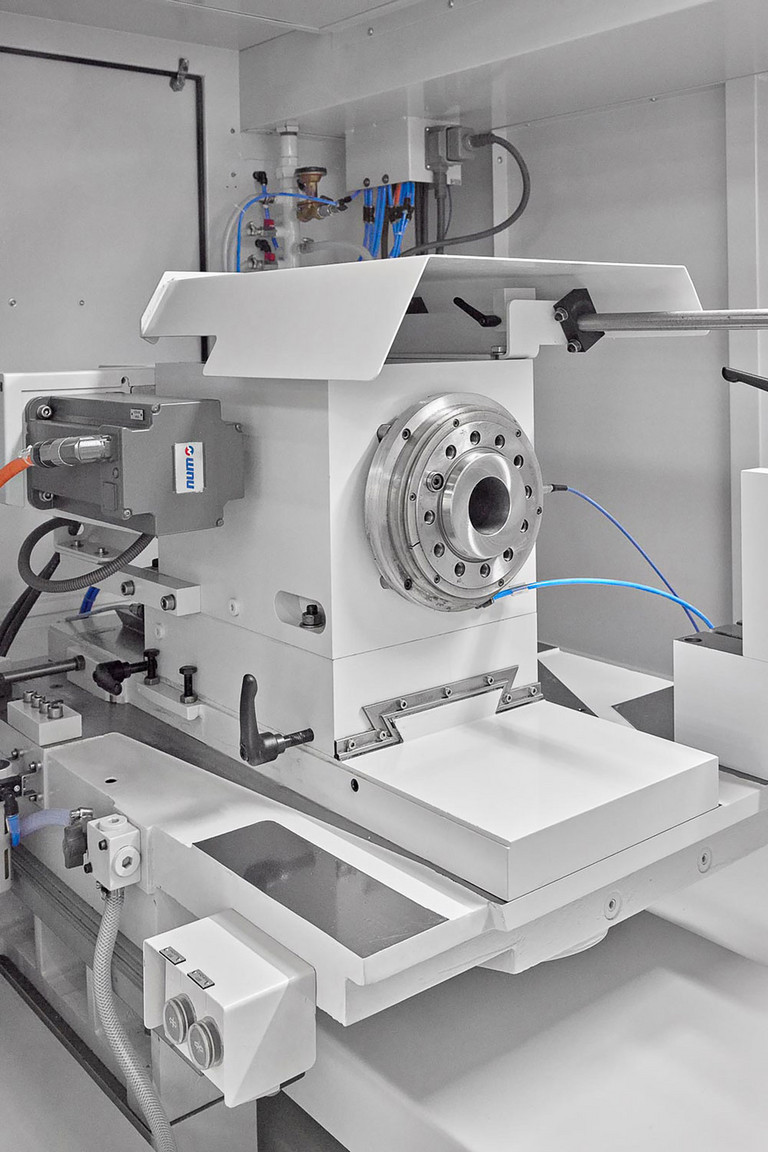
Défi de la rénovation
Jörg Huttelmaier répond également à la question générale de savoir s’il vaut la peine de moderniser de vieilles machines. « L’un des arguments en faveur d’une modernisation, outre les coûts réduits, est que l’opérateur connaît bien la machine et n’a donc pas besoin de temps de formation. L’encombrement reste le même et, en règle générale, les fondations peuvent continuer à être utilisées », explique Jörg Huttelmaier, qui ajoute : « La durabilité et le recyclage sont des sujets importants aujourd’hui. D’un point de vue environnemental, une modernisation est toujours une bonne chose, car l’empreinte CO2 est beaucoup plus faible qu’avec une machine neuve. »
Jörg Huttelmaier poursuit : « La modernisation ne consiste pas simplement à remplacer toutes les vieilles pièces par de nouvelles. Il s’agit plutôt de prendre une décision proportionnée et expérimentée quant au processus à utiliser et à l’endroit où il convient de le faire. Nos procédures de modernisation commencent toujours par une étude détaillée de la machine et une documentation de tous les dommages. Pour ce faire, la machine est entièrement démontée. Les différentes mesures et étapes de la révision générale et les exigences du client sont ensuite consignées dans un cahier des charges, qui est ensuite convenu avec le client.
Pour la Ceres 330, le principal défi n’était pas l’état de la machine, mais plutôt les exigences des programmes d’usinage, en d’autres termes, le système de commande. Dans un premier temps, il a été envisagé de remplacer l’ancien système de commande par un nouveau du même fabricant. Mais les adaptations de programme, indispensables pour Bruckner, auraient exigé un énorme travail de programmation, car il fallait, entre autres, des caractéristiques spéciales pour la rectification intérieure et le dressage. Or, cela n’aurait été possible qu’à un coût tout aussi énorme avec les progiciels autonomes fournis par ce fabricant.
Les spécialistes de HDC ont pu se faire une idée des besoins sur place avant le début du projet. « Chez HDC, nous avons nos propres programmeurs qui écrivent des programmes pour une grande variété de systèmes de contrôle. Mais dans ce cas, l’effort et les coûts associés dépassaient largement le niveau normal », explique Jörg Huttelmaier. « Notre évaluation a montré que nous avions besoin d’une CNC et d’un partenaire logiciel dont le système était suffisamment flexible et ouvert pour répondre à la large gamme d’exigences d’usinage que Bruckner avait pour la Ceres 330. »
Pour résoudre ce problème, Jörg Huttelmaier a utilisé ses contacts avec Marc Riedl, directeur des ventes pour le sud de l’Allemagne chez le fabricant de commandes et de logiciels NUM. Les discussions intensives ont révélé que NUM était exactement le bon partenaire pour l’application chez Bruckner.
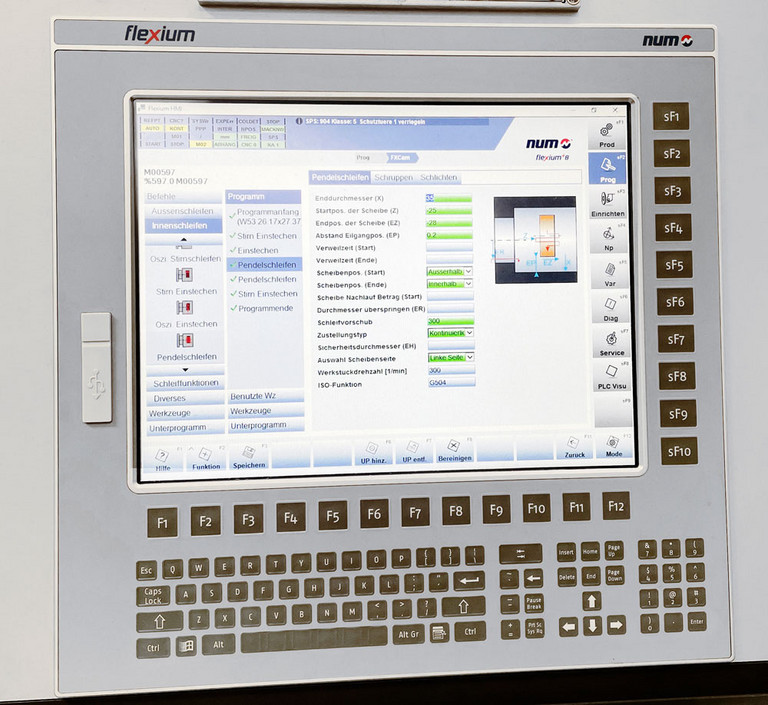
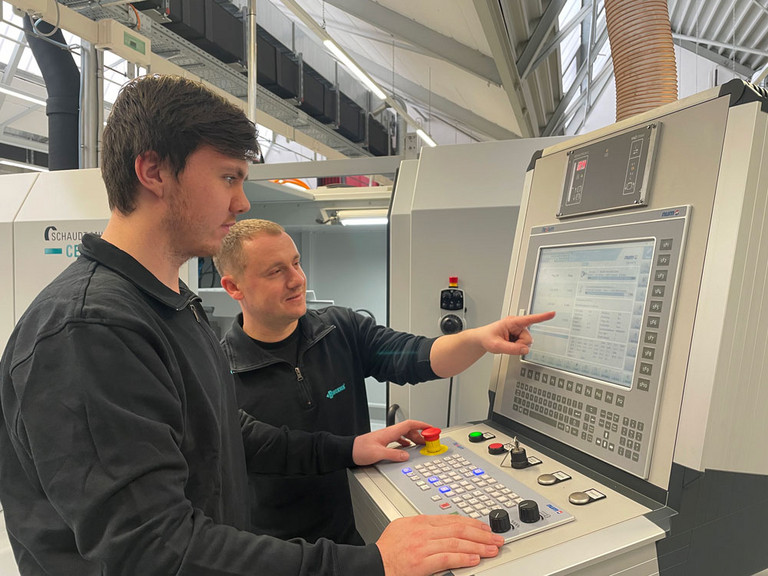
Un logiciel de contrôle qui ne laisse rien à désirer
NUM est présent dans le monde entier en tant que fabricant de solutions CNC haut de gamme et est particulièrement performant sur les marchés asiatiques, américains, français et scandinaves. En Allemagne, en Autriche et en Suisse, la société est principalement connue pour son logiciel de commande, qui est disponible dans différentes variantes pour le fraisage, le tournage, les opérations de rectification et le taillage d’engrenages.
L’entreprise suisse, dont le siège se trouve à Teufen, propose une large gamme de produits parfaitement adaptés, tels que des CNC, des amplificateurs d’entraînement et des moteurs. En outre, elle propose des formations, une assistance et des lignes de service. Les commandes CNC NUM se caractérisent par une ouverture totale du système à l’opérateur, ce qui permet une mise en œuvre facile de son savoir-faire et une adaptation parfaite à une large gamme de machines. Pour tirer pleinement parti de cette flexibilité, NUM fournit les outils de développement nécessaires, ou le personnel NUM peut mettre en œuvre des fonctions spéciales selon les spécifications du client et les mettre en service.
Chez NUM, l’accent est toujours mis sur les besoins du client. Cela signifie que les différentes IHM sont préconfigurées, mais qu’elles peuvent être adaptées en fonction de l’application. Une équipe de spécialistes de NUM se charge de ce travail de personnalisation. « Nos systèmes CNC évolutifs et flexibles de la série Flexium+ sont excellents pour le rétrofit car ils peuvent être parfaitement adaptés à n’importe quel besoin et à n’importe quelle machine », explique Marc Riedl. « Avec la prise en charge de plus de 200 axes, plus de 40 canaux, 4 000 E/S, plus de 1 Go de mémoire automate et plus de 30 Mo de mémoire programme, Flexium+ est facilement capable de contrôler les applications les plus exigeantes. Nous avons donc pu répondre facilement aux diverses exigences de Bruckner et intégrer tous les types d’usinage souhaités. »
NUM exploite trois centres technologiques indépendants avec des départements d’application où des solutions spécifiques aux clients sont développées, l’un d’entre eux étant situé à Holzmaden, en Souabe. « La particularité de nos trois centres technologiques est qu’ils échangent activement les uns avec les autres », explique Marc Riedl. « Par conséquent, les adaptations récurrentes des clients sont intégrées dans chacune des nouvelles versions qui sont lancées chaque année ; seuls les détails très spécifiques au client sont laissés de côté. De cette manière, nos systèmes ont toujours une longueur d’avance sur le marché. »
Le progiciel utilisé chez Bruckner est la solution de programmation d’atelier NUMgrind. Il offre une variété presque infinie de possibilités en matière de rectification et contient de nombreuses fonctions prêtes à l’emploi pour la rectification cylindrique et non cylindrique, ainsi que pour le dressage. Ces fonctions peuvent être facilement adaptées par l’opérateur aux besoins spécifiques de la rectification grâce à une programmation d’atelier intuitive et à une visualisation en 3D.
Les mesures de modernisation en détail
Le Ceres 330 était en relativement bon état, notamment en ce qui concerne les pièces en tôle telles que le carter, de sorte qu’une remise en peinture était suffisante. Lors de la révision mécanique, les vis à billes et le dispositif de recirculation des rouleaux ont été remplacés sur les axes X1 et Z1. Les pièces usées et défectueuses ont été remplacées dans le chariot de la broche et la poupée porte-pièce, ainsi que dans le système pneumatique, le système de lubrification huile-air et le système de refroidissement. De nouveaux systèmes de mesure absolue ont été installés.
L’équipement électrique, y compris l’armoire de commande, le câblage et le panneau de commande, a été entièrement renouvelé. En outre, de nouveaux moteurs et variateurs ainsi qu’une nouvelle commande numérique avec le logiciel approprié, ont été installés. L’ensemble des travaux a duré huit mois. Depuis juillet 2022, la Ceres 330 est à nouveau pleinement opérationnelle chez Bruckner.
Marc Sigle est très satisfait de sa nouvelle machine. « Tout d’abord, la machine est aussi fiable qu’une machine neuve en termes de fiabilité du processus, de répétabilité et de précision. Le logiciel apporte un soutien particulier à la rectification conique, dans le domaine de la rectification pendulaire de la face et de la rectification des deux côtés, ce que l’ancienne commande ne pouvait pas faire. La rectification des rayons et des contours est désormais possible sans problème. Les processus de rectification sont plus variables, la programmation est plus rapide. L’assistance sur site a été excellente, mais nous avons également beaucoup communiqué avec NUM via Team Viewer. »
La conclusion des trois partenaires ? « Un bon travail d’équipe », déclare Marc Sigle, qui fait l’éloge du projet commun. « La proximité de l’installateur HDC et la possibilité d’effectuer des tests à tout moment étaient uniques. » Marc Riedl ajoute : « Nous avons établi un bon partenariat pendant le projet et intégré les suggestions et les exigences du client au cours du processus. À l’avenir, les nouveaux développements de notre entreprise pourront facilement être intégrés chez Bruckner. De cette manière, le système de contrôle reste toujours à jour. » L’installateur Jörg Huttelmaier résume la situation : « Les défis à relever dans le cadre de ce projet étaient considérables. Mais lorsque les bons partenaires dotés du meilleur savoir-faire s’unissent, comme ce fut le cas ici, rien ne peut vraiment aller de travers. »
(Septembre 2023)