Supertec chooses NUM technology for its latest CNC cylindrical grinding machines
Innovative NUMgrind CNC software will help to simplify production of camshafts, crankshafts, cams, eccentric shafts, etc…
Supertec Machinery Inc., one of Taiwan’s leading machine tool manufacturers, has chosen to base new versions of its renowned Plunge type of CNC cylindrical grinding machines on NUM’s Flexium+ CNC platform.
Founded in 1954, Supertec Machinery Inc. has grown to become one of Taiwan’s top machine tool manufacturers. The company specialises in precision grinding automation and produces a diverse range of centreless, cylindrical and surface grinding machines. Based in Taichung City, Supertec operates sales and support facilities at strategic locations throughout Asia and Europe, as well as in the USA and South America.
Supertec has traditionally used Fanuc CNC systems for most of its machine tools. However, when NUM added non-circular grinding functionality to its popular NUMgrind cylindrical grinding software back in June 2020, the company realised that this innovative CNC technology provided exactly what many of its customers needed on their cylindrical grinders.
NUMgrind simplifies the creation of G code programs for CNC grinding machines through the use of a highly intuitive graphical human machine interface (HMI), and unlike conventional CAD/CAM workstation tools, it is designed specifically for use by shop floor personnel in a production environment.
After evaluating the software, Supertec immediately raised a purchase contract with NUM. According to Betty Chu, Supertec’s Assistant General Manager, “NUM has an excellent reputation in the grinding industry. Much like Supertec, this has been earned over many years. And the latest version of NUMgrind, which accommodates non-circular grinding, is a natural fit for our CNC cylindrical grinding machines. We also now benefit from very responsive local support – NUM’s Taiwan facility is less than 15 km away from our factory.”
Supertec’s Plunge type of CNC cylindrical grinding machines offer a choice of six capacities, covering distances between centres from 500 mm to 2,000 mm. The machines can also accommodate grinding diameters from 300 up to 430 mm (3 sizes), grinding wheel speeds up to 1,390 rpm and workhead spindle speeds from 30 to 350 rpm.
The new versions of these machines are based on NUM’s Flexium+ 8 CNC platform and use NUM’s high performance MDLUX drives and brushless servo motors for the X, Z and C axes. In addition to the NUMgrind HMI, the software that is being supplied by NUM includes the Flexium 3D simulator, which can be used offline or online, and an application-specific profile editor which enables users to import DXF files.
Johnny Wu, General Manager for NUM Taiwan, points out, “The ability to use the Flexium 3D simulator both offline and online provides Supertec’s customers with a distinct advantage. CNC programs can obviously be prepared offline and checked for potential problems such as collisions before being transferred to the machine. But the simulator can also be used online. This enables operators to gain vital visibility of the grinding process – which is normally obscured by the flow of oil.”
The new machines will be introduced to the public at the next opportunity, which will likely be TMTS in 2022 due to Covid-19 restrictions.
Technical background
Non-circular grinding is used in a wide variety of automated manufacturing applications, such as the production of camshafts, crankshafts, cams and eccentric shafts. However, it is an extremely complex task, because the non-circular contour leads to constantly changing engagement and movement conditions between the grinding wheel and the workpiece.
Using the non-circular grinding function of NUMgrind, the closed shape of the workpiece is defined in the XY plane. Grinding is then performed by interpolating or synchronising the X axis with the C axis (workpiece spindle). Axial movement in the Z axis can also be accommodated, by means of oscillation or ‘multi-plunging’. The Flexium+ CNC system’s NCK transforms the contour from the XY plane into an XC plane, and calculates the corresponding compensation and in-feed movements, taking the grinding wheel diameter into account. The speed profile is also transformed, so that the speed and acceleration are automatically adapted to suit the physical attributes of the machine.
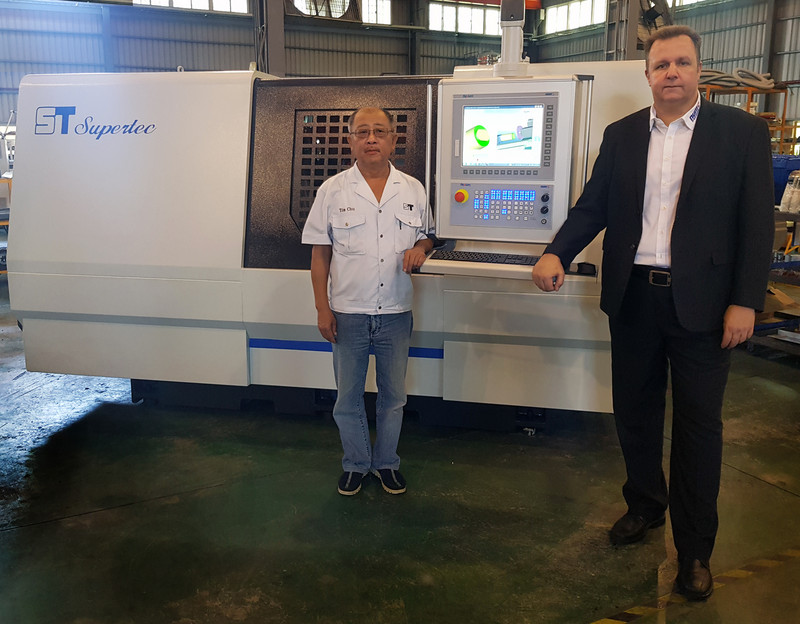

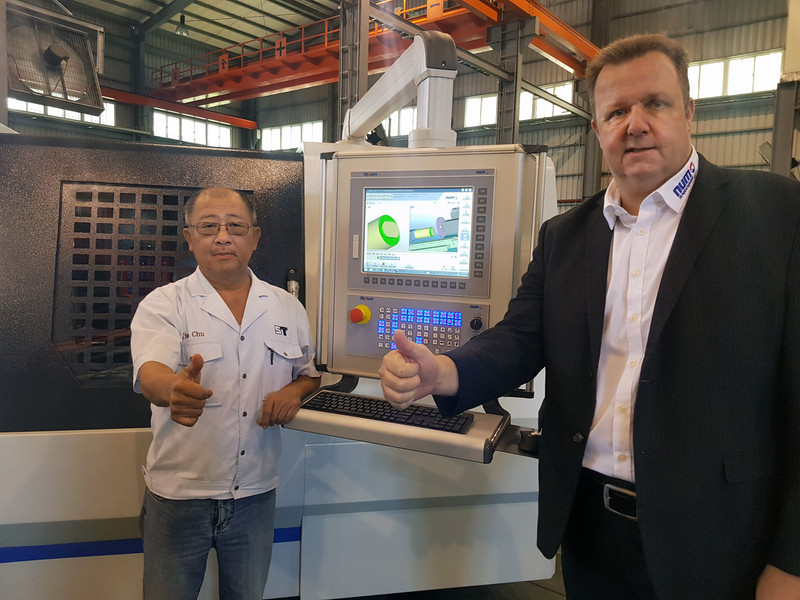