NUM 通过配备人性化控制杆的 6 轴 CNC 控制埋弧焊系统 专利为 Richter Maschinenfabrik AG 提供支持
带 6 个插补轴的 CNC 控制轮廓埋弧焊系统采用 NUM 提供的高端 Flexium CNC。该系统采用控制杆进行操作,便捷控制且快速易学。通过确定几个示教点,以便直接从组件本身获取复杂的焊接轮廓。操作人员只需触摸按钮即可随意调整焊接路径,这使得在复杂的曲线轮廓上进行 CNC 自动化多层焊接成为可能。
埋弧焊工艺本身并无新颖之处 - 它是一项既定的技术,用于在大型组件生产过程中实现高品质焊缝。而由 Richter 与 NUM 共同开发的系统的独特之处在于将市场上的各种机床组件进行组合,并且这些组件能够基于 CNC 及专门开发的应用进行完美互动。因此其能够提供始终如一并且远远超过常规方案的卓越焊缝质量。
埋弧焊系统的焊头与焊丝及送粉装置一起安装在可水平移动的悬臂上,可向各个方向旋转并上下调整。这意味着焊头可定位在焊台上方的任一点。悬臂上集成了包含带功能键的FS152 显示器的系统控制单元、座椅和控制杆。从设定到工件加工的所有系统命令及设置均使用该控制杆执行。在生产过程中,这不仅提供灵活性,而且具备相当大的人体工程学优势;焊工可戴上手套操作机床,同时简化了复杂的机床控制,无经验的焊工也能在几个小时内独立操作和工作。该简单控制装置及所连接的控制器由 Richter 和 NUM 的现场技术人员精心开发,并基于各项实践测试予以完善。控制杆发出的命令由 Fxleium CNC 通过 6 个轴转换为运动。
待加工工件被放置在悬臂下方的 60 吨大型旋转倾斜工作台上。顾名思义,该工作台可持续旋转,最大倾斜至 45°,这样就能焊接非水平位置的接缝。可旋转悬臂的另外一个优势是能够完全推到一边。这意味着可对尺寸超出转盘的大型组件进行焊接。
之前,埋弧焊系统通常用于焊接 V 型或 X 形直线接缝。直到现在,仍需使用其他焊接方法 (MAG) 手动进行轮廓焊接,这意味着耗费大量的时间和精力,并且尤其需要避免质量波动(气孔的形成)。而现在这款新型埋弧焊系统可自动焊接轮廓。它实现了真正意义上的时间节省,同时不会影响质量。“总的来说,我们所开发的这款新型埋弧焊系统表明,将生产性能提高 25% 至 30% 左右是完全合理的,”Richter AG 电子部门主管兼本系统开发人员 Dirk Kunig 解释道。
Richter AG 的工作准备及焊接监测部门几乎每天都能发现该系统的新应用方式,这在以前是不可想象的。Dirk Kunig 证实:“性能和质量方面实现了重大飞跃。”
复杂的系统控制由 NUM 提供的Flexium 68 CNC 单元进行处理,但是用户不会察觉。随系统提供的用于操作设备的标准 NUM HMI 已通过专为此机床而开发的应用大大简化。仅用控制杆就能进行控制。焊工可在示教过程中使用控制杆绘制出需创建的焊缝,同时这些示教点被读入系统。
未来我们计划如同上一期 NUMinfo 中报道的火焰切割系统,用数字化方式将示教点传输至埋弧焊系统,从而帮助焊工彻底消除手动加载的麻烦。这会节省更多时间。从显示器上可以看出,菜单项已合理排列,可使用控制杆进行选择。显示器上的底部按钮及颜色安排与控制杆上的按钮一致,可在不同的菜单项或菜单级之间切换。
在后台,CNC 控制加工焊缝的焊头位置,另外一个 CNC 通道控制焊丝的推进及焊剂送料装置的运动,使其始终先于焊缝过程。即使由不同材料制成的组件,例如厚钢板和重型铸件也可完美焊接,不会产生错误且能够达到所需精度。采矿业中的巨型挖掘臂通常需要使用该类由不同材料制成的大型组件。
凭借这一新型的埋弧焊系统,Richter Maschinenfabrik AG 通过与 NUM 的密切合作,向提高焊缝质量、加快焊接速度和节省焊接时间及显著降低埋弧焊生产成本迈出了重要一步。并且再次证实,如果两家公司分享其专业知识以创造新的东西,则能获得超越预期的成功。
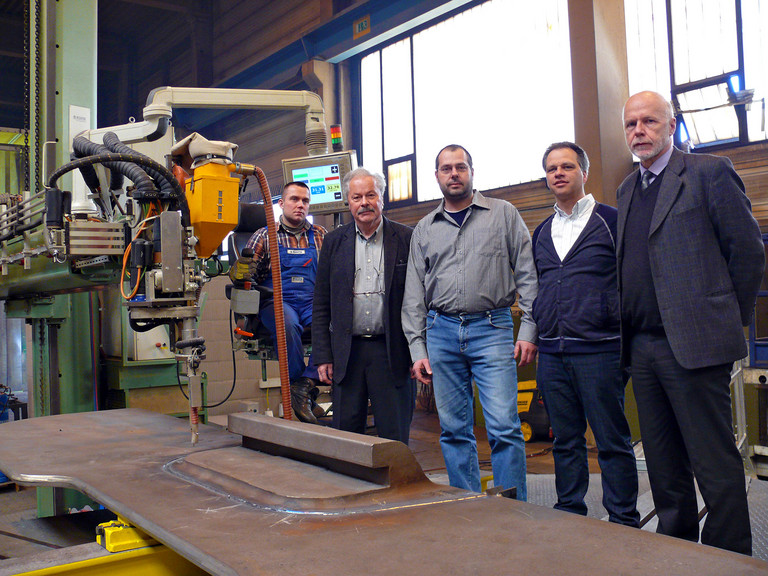
(九月 2013)