American Successes
NUM Corporation enjoys considerable success in the North American market. Here we take a brief look at three recent build-ins.
Anderson-Cook Machine Tool
Anderson-Cook Machine Tool is the world's leading manufacturer of spline-rolling machines and associated tools. Based in Fraser, Michigan, this company is a relatively new account for NUM Corporation, having first approached us in March 2009 for a CNC system for an innovative 3-axis precision grinding machine that it was developing. The machine was launched just three months later, and is already enjoying considerable market success.
Anderson-Cook’s new C3-5-F AC-Tru precision grinding machine is capable of form grinding, plunge grinding and in-feed grinding, and features a built-in acoustic system for polishing to a high micro using carbide or steel. The machine incorporates a novel ‘AC-Tru Centerless’ grinding fixture, which can accommodate a very wide range of work-piece diameters, from 0.127 mm (0.005 in) to 139 mm (5.500 in).
The AC-Tru Grinder has three precision axes - a 558 mm (22 in) longitudinal table, a 203 mm (8 in) cross slide table and a 368 mm (14.5 in) vertical column - each equipped with an AMO digital scale which provides 500 nanometre (20 millionths of an inch) accuracy. The two horizontal axes employ precision linear rails and are driven by high performance digital linear servomotors, which combine exceptionally high positional accuracy and repeatability with a very long service life. As standard, the AC-Tru Grinder is also equipped with a 5 hp professionally balanced spindle, controlled by a variable speed drive. The spindle can accommodate wheel diameters up to 30 cm (12 in) and can attain speeds up to 3,600 rpm - the equivalent of a linear speed in excess of 57 m/s (187 ft/s).
All three axes are controlled by a NUM Power CNC system, and the machine's HMI comprises a NUM FS151iCF operator's panel and an MP03 machine tool builder's panel, co-mounted on an articulated ergo arm. The NUMgear machine control software includes the NUMPass and PCProCAM packages for cylindrical grinding. The control flexibility of the AC-Tru Grinder's software enables the machine to handle a wide variety of grinding processes, including centre-less thru-feed and plunge, multi-plunge mixed with an oscillation cycle, OD profile, surface and creep feed.
According to Mike Vettraino, Grinding Product Manager, of Anderson-Cook Machine Tool, "The user interface of NUM's CNC software combines easy-to-understand graphics with straightforward parametric programming, making it highly intuitive. This helps to reduce the time and cost overheads of operator training, and enables our customers to bring the AC-Tru Grinder on-stream very quickly."
Bourn & Koch Machine Tool Company
One of NUM Corporation’s very first customers, the Bourn & Koch Machine Tool Company is nowadays a highly valued business partner. Based in Rockford, Illinois, Bourn & Koch operates a large, 12,000 m2 (130,000 square feet) purpose-built manufacturing facility, where it produces an extensive range of precision machine tool products. The company also rebuilds and remanufactures legacy machines, retrofitting many of them with NUM CNC systems to improve their performance.
According to Loyd Koch, Vice President of Bourn & Koch, "We have been utilizing NUM controls in our products for over 20 years. The initial driving force was that NUM produced the only control system with an integral electronic gearbox that met our requirements for gear hobbing and grinding. Over the years, this usage has expanded to other parts of our business - including turning, milling, boring and grinding machines - due to the cost, support and complete product solutions offered by NUM Corporation."
Bourn & Koch's latest gear manufacturing machine - the 400H Series II horizontal gear hobber - is a highly advanced seven-axis CNC system capable of exceptionally high throughput. As standard, the machine is equipped with NUM's Axium Power CNC system and FS151iCF control panel - which features an integrated industrial PC - and makes extensive use of NUMDrive C compact servo drives and BPH series brushless axis motors with absolute feedback.
The supplied NUMgear software features a multilingual user interface, which provides Bourn & Koch with a significant competitive advantage for machines that are exported to other countries, and includes the NUMPass and PCProCAM packages for gear hobbing. Custom hobbing screens enable multiple hobs to be used to produce cluster gears within the single setup; the CNC hob-shifting macros simply shifts from one tool to the next, while maintaining synchronization to the gear to allow for tooth line-up. The 400H series gear hobber can accommodate a work diameter of up to 400 mm (16 in) and features a unique CNC servo-driven tailstock.
The tailstock can be programmed to have two pressures for each cycle; a high pressure is used initially, to embed the face drivers into the part, and then a lower pressure is used during the actual cutting operation, to prevent the drivers from going deeper into the part and causing a small amount of rotation that would show up as lead error when the gear is inspected. The NUM digital drive interface enables the tailstock motor's torque output to be adjusted on-the-fly, to provide programmable set points for the tailstock pressure.
Star Cutter Company
Founded in 1927, Star Cutter Company has grown to become a world leader in the cutting tool industry. Headquartered in Farmington Hills, Michigan, the company operates numerous product-specific manufacturing facilities throughout the state. Star Cutter chose to adopt NUM CNC hardware and NUMROTOplus software for its latest tool and cutter grinding machine.
Star Cutter's new NTG tool and cutter grinder is designed for manufacturing and reconditioning complex cutting tools quickly and precisely. Typically, these tools would include end mills, drills, step drills, taps and form cutters. The NTG is a five-axis grinding machine - featuring a three-station wheel and manifold changer capable of switching grinding wheels within 10 to 15 seconds - complete with a fully integrated 3-axis automated loading and unloading stage. The high speed auto loader holds up to 288 parts, and can load and unload 12.7 mm (0.5 in) diameter, 200 mm (8 in) long tools to/from an automated tailstock centre in less than 15 seconds.
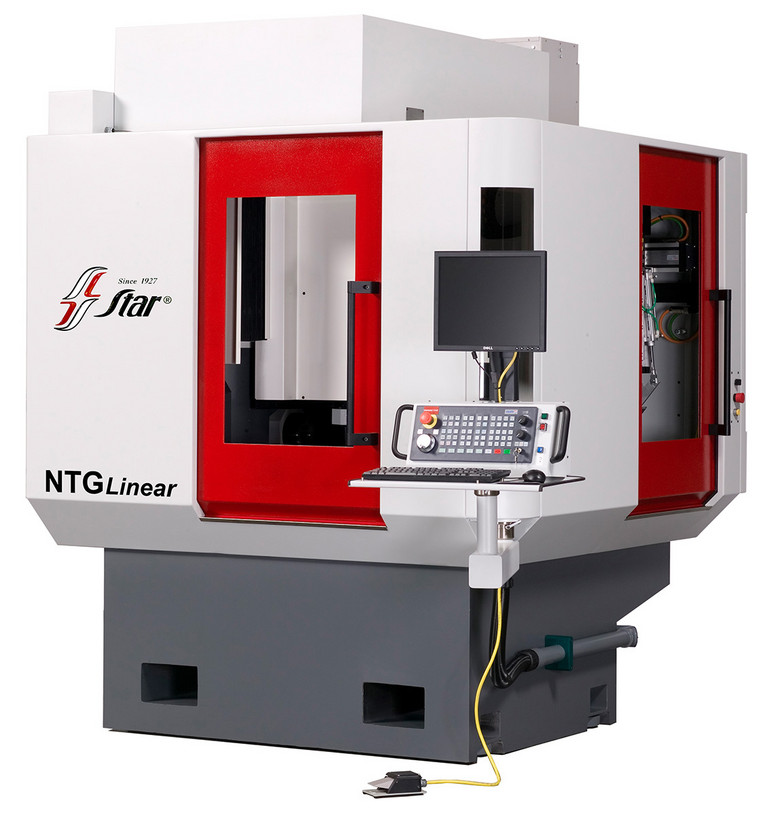
All eight machine axes are controlled by a single NUM CNC system. The machine also makes extensive use of NUMDrive C compact servo drives - their small size is an important advantage, because the NTG is designed to take up minimal floor space - and employs linear motors on two of its horizontal axes to maximize performance.
Linear motors on two horizontal axes eliminate the need for ball screws and reduce the number of moving parts, lowering maintenance costs and improving surface finishes. And, since the loader is integrated in the standard enclosure, the NTG takes up 30% less floor space than earlier generation machines. NUM's NUMROTOplus software, designed specifically for tool production and re-sharpening tasks, enables the machine operator to easily check and optimize tool alignment via a graphical HMI.
Star Cutter will be exhibiting its new NTG tool and cutter grinder at IMTS 2010. Check out Star-SU booth N-6924 in the North Building.
(August 2010)