Ultra Fast Interpolation and Near Absolute Vacuum
From the depths of the ocean to the farthest reaches of the atmosphere, from parts weighing just a few grams to those requiring nearly a megawatt at the spindle, from clocks and watches to gears over a meter in diameter, from machines for mass production to those designed to be used only once, there are few areas that NUM has not addressed.
A new frontier has been crossed with TECHMETA Engineering; this time in the field of near absolute vacuum with the realization of electron beam welding machines.
Founded in 1964 and located in Haute Savoie, France, TECHMETA Engineering is the world leader in electron beam welding machines. This vacuum welding process does not require the addition of material, the welding being done by melting the metal of the part. The result is high quality joints, without oxidation or pollution from the environment, and welds that can reach significant penetrations, thus guaranteeing excellent mechanical properties. In addition, thanks to the single-pass process, the deformation of the part is minimal, which often makes post-welding machining unnecessary. The fields of use are numerous: defense, nuclear, aeronautics, automotive and research. In order to facilitate its export development, which represents nearly 80% of its production, and to focus on its know-how, TECHMETA Engineering needed a reliable and trustworthy partner for high performance CNC systems. After a test campaign where numerous challenges were met, TECHMETA Engineering decided to adopt a collaborative approach with NUM.
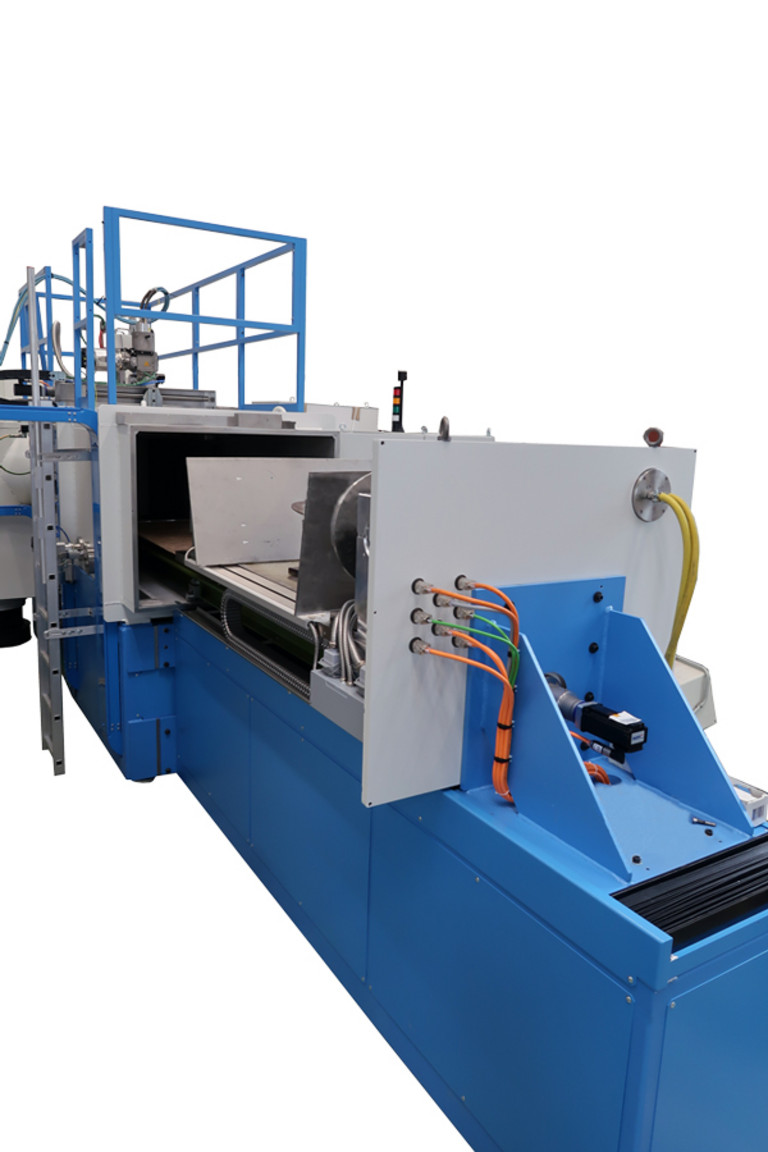
The basic principle of electron beam welding may seem familiar to those who knew television before the advent of LCD and LED versions, but the magnitude of the parameters involved bears no similarity to those of our old television set. A cathode, heated by a filament and brought to a potential of several tens of kilovolts, will emit electrons (at a few hundred mA) that will strike the part to be welded at a speed of several km/s. On their path, these electrons will encounter several devices designed to modulate the intensity of the beam, then focus it and eventually make it vibrate according to a well-defined profile before its impact on the part with such energy that the metal will melt locally. All these parameters, as well as the positioning of the part, must be able to evolve during the process, which takes place in a quasi absolute vacuum.
Before the more sophisticated functions could be used, it was necessary to ensure that the Flexium+ system was compatible with the environment. Knowing that even the earth’s magnetism affects the beam path, it is necessary that the motors do not create disturbances and that they are compatible with vacuum operation. This ranges from the ability to limit heating, where convection is by definition impossible, to the absence of electromagnetic radiation, to the lubrication of the bearings. NUM’s motors meet these criteria perfectly, and their ability to connect to a single cable limits the number of interfaces between the atmospheric and vacuum zones. The adaptability of NUM’s equipment also helps to avoid the risk of electrical ignition, which reaches a maximum at a certain pressure value: at 10-2 atm., 300 V is sufficient to create an arc between two elements a few mm apart (Paschen’s law).
Of course, it took more than excellent hardware features to make Flexium+ a success. The project in question, for an Asian customer, includes five machines with well-defined requirements.
The fine control of the electron gun parameters (intensity, acceleration, focusing, etc.) in real time while the workpiece is moving continuously does not pose any particular problems thanks to the symbolic programming and the customizable G functions. However, to ensure a perfect weld, it is not enough for the impact point of the electron beam to follow the defined trajectory precisely; all the expertise of the manufacturer and the welder comes into play here. This point of impact must, depending on the case, be able to “vibrate“ around the theoretical point, not in a random way but on the contrary according to a selected or programmed profile as well as at a programmable frequency. The elements of this vibration trajectory can be of the order of ten µs, which is far from the usual interpolation capabilities. By means of additional deflection coils, the Flexium+ system will impose all the desired characteristics on the beam. These beam control values are known as “electrical axes“, and it is thanks to the power and modularity of NUM’s numerical control system that such high performance has been achieved, but we won’t go into that here. There remains the calculation of the parameters, particularly for the vibration path, which was far from being the least challenging. Flexibility and openness of the system also facilitate the bidirectional dialogue with a vision system that serves both to accurately locate the position of the beam (sensitive to the slightest magnetic disturbance) and to monitor the parting line. Any deviations are corrected in real time by dynamic operators.
The whole setup also includes a supervisor running on an FS194i which, in addition to generating ISO programs with up to 512 cells, controls the parameters of each weld (vacuum, speed, focus, deflection etc.) and ensures the traceability of welded parts.
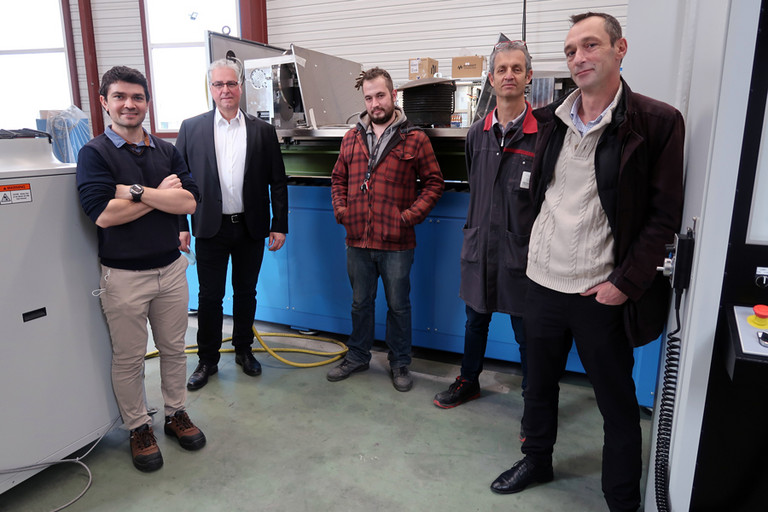
Mission accomplished for Flexium+, but what is the customer’s opinion on this case? Mr. Vaudaux and Mr. Creton from the design office said they appreciated the modularity of the system and the ability to communicate with additional elements, as well as the integration tool (Flexium Tools), which allows the entire installation to be programmed and set up using a single software package. The technical director, Mr. Betemps, emphasized the quality of the relationship with NUM, which has always been able to provide the necessary support and answers. This is in line with NUM’s philosophy of providing the best hardware, software and service to enable our customers to develop their competitive advantages in a partnership approach. As Mr. Barsanti, Director of NUM France, says: “The power and flexibility of our products, combined with the experience of our engineers, have enabled us to offer TECHMETA Engineering a first class solution, but make no mistake, this is a story about people who are passionate about their work.”
(September 2022)