Market leader in CNC dressing and profiling machines - A long-standing, successful, cooperative partnership with NUM
The focus of Rudolf Geiger Machinenbau GmbH lies on the development and design of CNC controlled dressing and profiling machines. For some time, Rudolf Geiger Machinenbau GmbH has been the market leader in the area of dressing and profiling of CBN and diamond wheels up to 800 mm. The consistent use of NUM CNC control systems on all machines delivered is an important part of our success. This long standing synergy between the two companies results in an even greater value to Geiger’s customers.
Geiger has been using the NUM CNC control systems from the very start, which is about 20 years. “For our CNC machines, we want to use a control system that our clients in the tool grinding sector are already familiar with and use, which is why we chose to work with NUM,” explains Georg Marvakis, CEO of Geiger. Clients know the easy operation, functionality and the quality of the NUM CNC control systems from the tool grinding sector because that is where NUM has been market leader with its NUMROTO for many years. This also means that there are no additional costs in terms of time or employee training for Geiger clients when it comes to working with Geiger dressing or profiling machines.
The Geiger dressing and profiling machines are used worldwide. Most of the machines are in Europe, USA, India and Asia. Because NUM maintains an international service network, the synergy can be used in the best way possible - ultimately to the advantage of clients thanks to quick problem solving at the end customer - by shorter downtimes and therefore limited loss of production. Apart from the development and design of standard and special machines, Geiger is a user as well and offers services like contract production, high-precision CNC milling, turning and grinding with up to 6 driven axles, laser structuring and labeling or production of precision parts for the medical sector.
True to the Geiger motto “Precision is our passion and constantly takes us further”, the focus of Rudolf Geiger Maschinenebau GmbH lies on the development and design of high-precision CNC dressing and profiling machines with an accuracy range below 2 μm. By consistently upholding this precision, Geiger has managed to conquer the leading market position in this specific segment. For all new designs, Geiger systematically uses the NUM high-end product, the Flexium+ control system, putting Geiger at the top in automation technology as well. Allowing the end customer to use the entire spectrum of possibilities offered by the NUM Flexium+ CNC control system.
A precision grinding wheel is an important element for the tool grinder in tool production, because precise tools can only be produced over a longer period of time with a smartly dressed grinding wheel. Many tool grinders dress their grinding wheels inside the tool grinding machine. However, this results in downtime of the expensive tool grinder because while being dressed, no workpieces can be produced. By investing a dressing and profiling machine, the wheel dressing takes place parallel to tool production and the fully dressed grinding wheels can be inserted into the tool grinder as needed. The downtime for productive tool grinder is reduced to the minimum.
The AP900 CNC dressing and profiling machine, shown here, dresses grinding, with a wheel diameter of up to 800 mm and accurately work with a maximum weight of up to 150 kg per wheel. The maximum width that can be dressed with this machine is 200 mm. The AP900 can also be loaded with a crane: A very important attribute since wheels can weigh up to 150 kg. Machine stability should also be emphasized since it ensures that the grinding wheels become perfectly round and have no nicks. This stability is achieved by the weight of the machine (almost 4 tons) and by constant improvements to the special design.
The software used on the AP900 was developed by Geiger in-house. It is menu driven and specifically adjusted to the eventual user of the dressing and profiling machine. “It is easy to use and self-explanatory. An operator can become proficient within 4-6 hours,” Johann Kutzberger, the software developer, adds. By means of a simple ‘teach-in’ for the grinding wheel, anyone can independently perform dressing and profiling on the machine within a short period of time.
The data for dressing and profiling a grinding wheel can also be directly transferred from the tool manufacturer as a DXF file. The DXF file is then read into the dressing and profiling machine so that the grinding wheel can subsequently be dressed precisely. Using the reference values, the grinding wheel can also be measured and reworked if necessary.
The AP900 also has an automatic dressing function, meaning that multiple identical grinding wheels can be dressed one after the other. All that needs to be done is to set up the data and then let the machine work through each grinding wheel on its own until the end of the process. The operator simply changes the wheel and returns the AP900 to zero, and starts the next cycle.
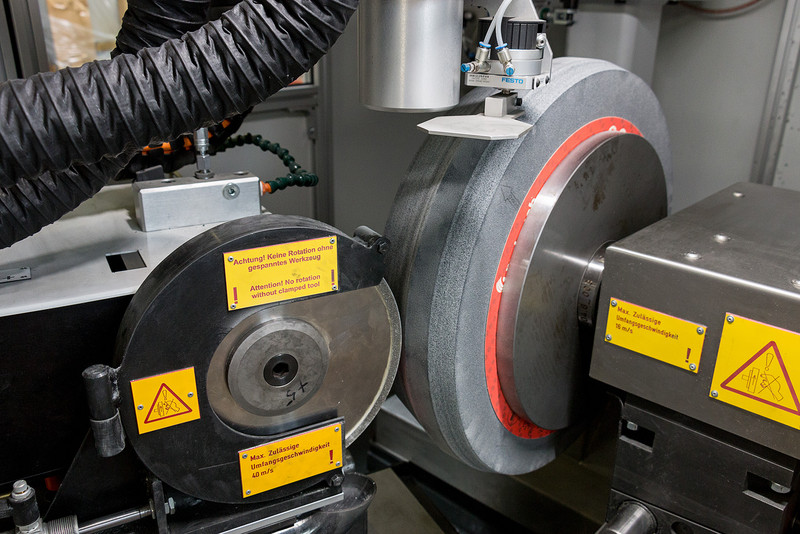
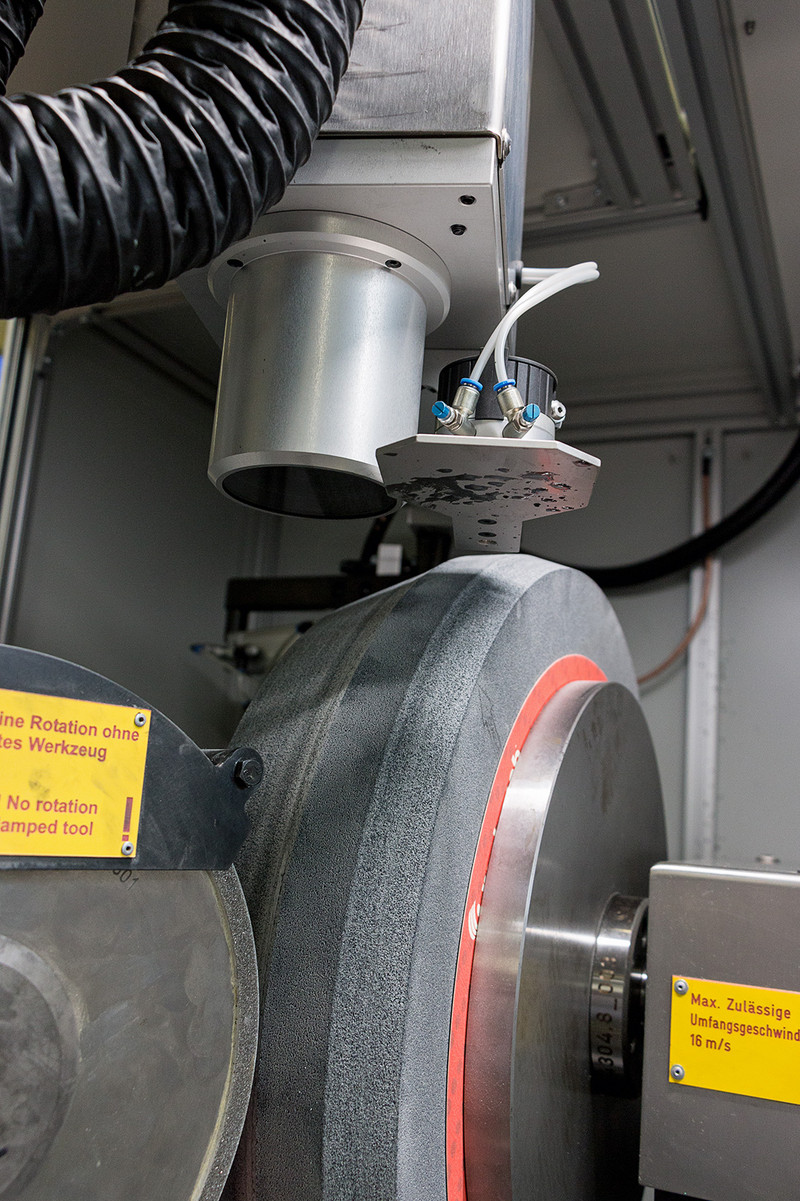
The AP900 uses silicon wheels to process CBN or diamond wheels. The silicon abrades the adhesive material in the grinding grains/diamond grains until, again, there are enough grinding grains/diamond grains in one line present on the grinding wheel. So the wheel is dressed again and sharp for use in the tool grinder.
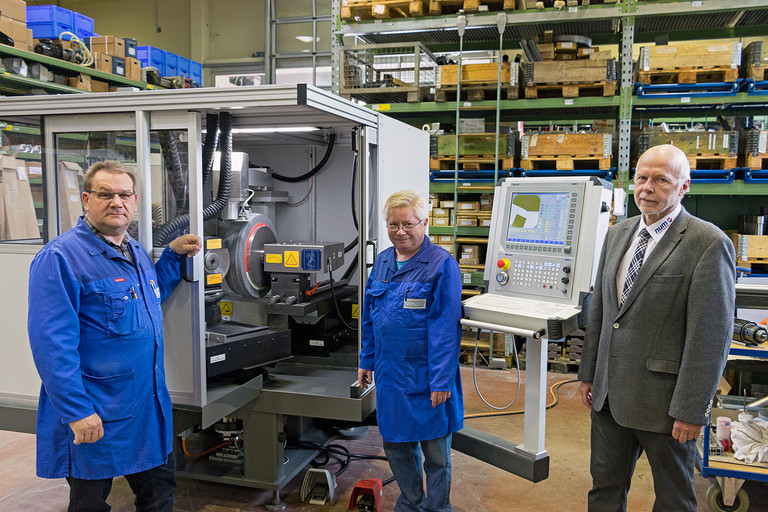
Having software development in-house is another advantage of Geiger. It allows the company to meet specific demands of clients. Thanks to the long-standing, close partnership with NUM, even more complex special CNC machines can be customized, designed and built for clients. The AP900 proves once again that close collaboration between niche partners creates a competitive advantage in the market.
(September 2017)