Machine Control in Virtual Realities
elumatec AG has set up a system for virtual commissioning of its control software. This significantly shortens the test times for the software on the real profile machining centers. The NUM Flexium+ CNC platform was structurally adapted for the system.
“Our programmers are now allowed to test everything they have previously tested on a machine on the digital twin. Only then can they apply their program to the real machine,” says Felix Schlachter, head of software development at elumatec AG, summarizing the result of a project in which a system for virtual commissioning was set up for elumatec’s SBZ 151 rod machining center. Core elements are the ISG-virtuos simulation platform and the NUM Flexium+ control system.
The company and its products
elumatec AG in Mühlacker builds and develops saws, milling machines, corner crimping presses and bar machining centers, suitable measuring and stop systems, assembly and logistics equipment, and software. The approximately 700 employees worldwide support around 30,000 customers and generate annual sales of around 125 million euros. In the bar machining center (SBZ) product area, the company specializes in machines that finish profiles made of aluminum, plastic or thin-walled steel. CNC-controlled, they perform operations such as milling, drilling, tapping, thread milling, notching and sawing to a high quality standard. The SBZ 151 5-axis machining center has proved particularly popular, with over 60 machines sold each year. The series, which has been available since 2006 and has been continuously modified, is used in classic metal construction as well as in industrial companies and the automotive sector; other user sectors include rail vehicle, body and trailer construction as well as office furniture construction and shipbuilding. The machines mainly process profiles with lengths of 6-15 meters. These usually come directly from the press shops and are processed into finished parts on the rod machining centers.
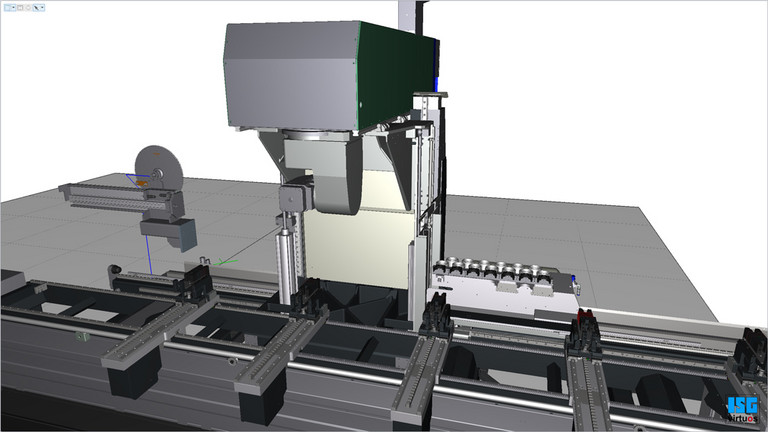
“With these profiles, the challenge is to ensure consistently high quality at high speed in profile machining over this length,” emphasizes Felix Schlachter. To achieve this, the SBZ 151 works with stationary profiles clamped on the work table and a movable machining head complete with automatic tool changer and tool magazine. Regardless of the length, in practice each profile has different requirements for handling, clamping and machining. For this reason, elumatec’s application engineers first check for each prospective customer in their test center whether all customer requirements can be implemented on the customer profile with a standard machine. If this is not the case, we adapt the machines to the end product for the customer,” says Felix Schlachter. In some cases, this can be done with additional equipment and/or adjustments to the control software are sufficient. Thanks to the possibility of parameterization in the NUM Flexium+ CNC system, most adjustments can be realized by changing the corresponding parameters without modifying the series software. “This is the flexibility we bring to the table. We deliver the SBZ specifically optimized for the customer, but for us it is a standard machine,” emphasizes Schlachter.
Until now, software adjustments or changes at elumatec involved time-consuming tests on the real machine. With the new system for virtual commissioning, this is largely shifted to the office workstation. The system is based on a kinematic simulation of the CAD model of the SBZ 151 on the ISG-virtuos simulation platform and its connection to the real control system.
“We map the control components one-to-one in our system. Together with the control computer unit, we interconnect everything that is done virtually via the system bus. We make this real controller believe that the system bus is fully equipped as if it were connected to a machine,” explains Felix Schlachter. In fact, however, there are no real drives or IOs connected to the EtherCAT, but rather another PC that simulates them. “This allows us to program as if we were at the machine, without having to adapt the programming for this,” adds the software developer. On the one hand, this relieves the programmers because they can program without the risk of a real crash, and on the other hand, the programs also work on the real machine right away.
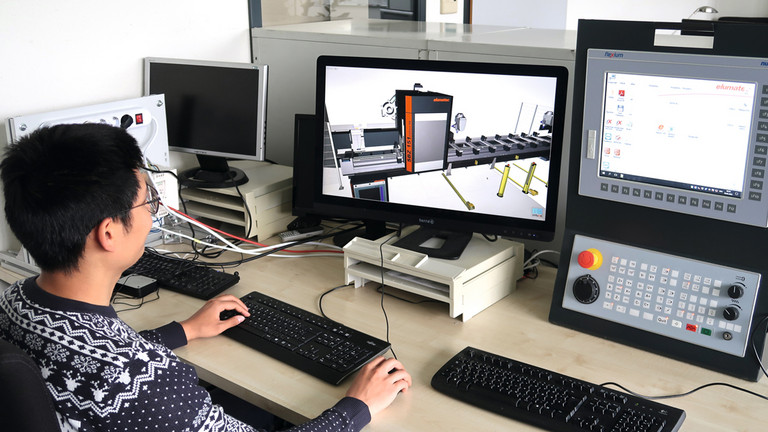
The development team at elumatec developed the system in close cooperation with NUM. For 20 years, elumatec has been working with NUM controls and uses almost the complete product range of NUM’s Flexium+ CNC system in the SBZ 151, from the drives to the control computer. In this respect, it was thanks to both the many years of close cooperation and the convincing presentation of the elumatec project, that NUM made some structural changes to Flexium+ , which included connecting the ISG-virtuos simulation platform.
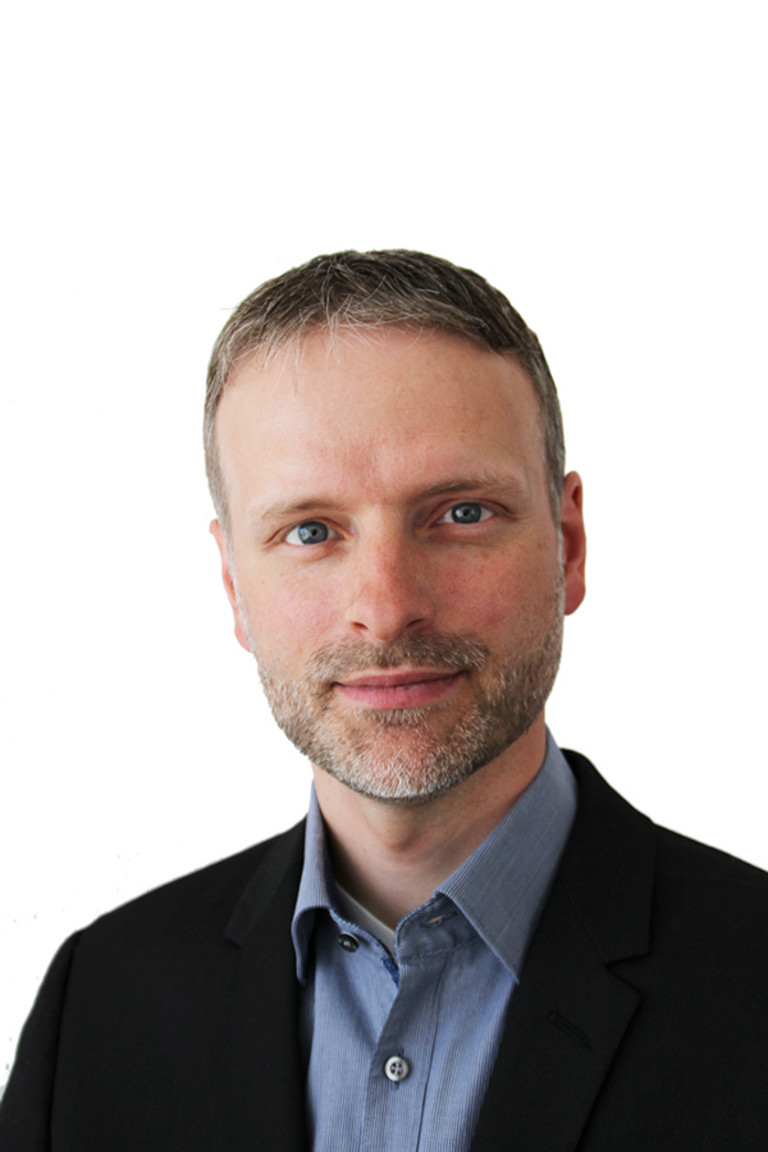
Digital twin instead of real machine
“It is important to us that we have the SBZ 151 as a digital twin and do not always need the machine in physical form”, emphasizes Felix Schlachter with regard to the future of the project. This will be expanded, he adds. Everything that is available on the machine and everything that elumatec obtains from NUM on the hardware side will be simulated in the future.
The potential applications of the digital twin and virtual commissioning seem enormous. For example, troubleshooting on machines that are running in production at the customer’s site is very promising. “We then get all the relevant data from the customer, play it into ISG-virtuos and virtually track how this error occurs. This is actually very practical and it works well,” explains Schlachter. In addition, new employees can be trained on the digital twin without blocking the real machine. Even studies to determine the machining times of certain profiles can be carried out virtually, by importing the CAD profile data into the simulation platform, where machining takes place virtually in real time.
“In the case of additional equipment, special designs or even robot connections, the digital twin also gives us a head start in terms of time,” says Felix Schlachter. “We can start developing the software immediately after designing with the digital model, without waiting for a special design to be physically built.“
Automation and standard interface
Robot connections in particular will play a greater role in the future, as demand for them is increasing. “But at present, we only use robots in special individual cases, but an interface integrated in the standard machine is available.” Thus, elumatec is open to third-party automation projects, as was recently the case with the integration of an SBZ 151 into a robot cell for automatic loading and unloading of the machine. On the control side, the robot cell acts as a master that interacts with the SBZ controller. The overall system is then operated via the cell controller, which in turn prompts the SBZ controller to process certain orders, for example. In this project, elumatec was able to take advantage of the flexibility of the NUM controller on the software side to adapt processes for connecting robots and ultimately develop a standardized robot interface. “We now know how a robot connection works, and we can interact with robots. We have created a document that says what signals we provide to the robot at the interface. This means that everything is standardized so that it can be implemented in a reasonable project time,” sums up Felix Schlachter. If adjustments are made to the connection, the digital twin will be used to ensure high software quality.
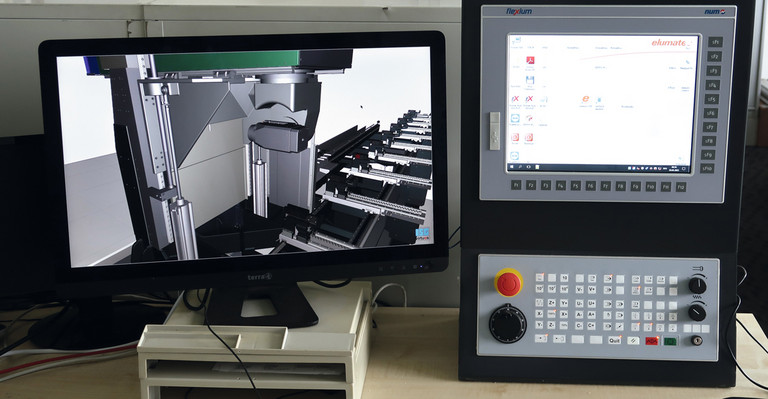
(September 2022)