Production Research: Highest dynamics and precision in series production
The best processing machines currently existing provide production research with the basis for further technological leaps. The accuracy and speed of a test machine made by Anger, equipped with NUM, was enhanced, tested and has now come into operation for ongoing research projects.
Profactor Produktionsforschungs GmbH, based in Steyr, Austria, is working on production technology for the future. The production of composite materials such as magnesium/aluminium, steel/magnesium or plastic/wood, is a central area of concern.
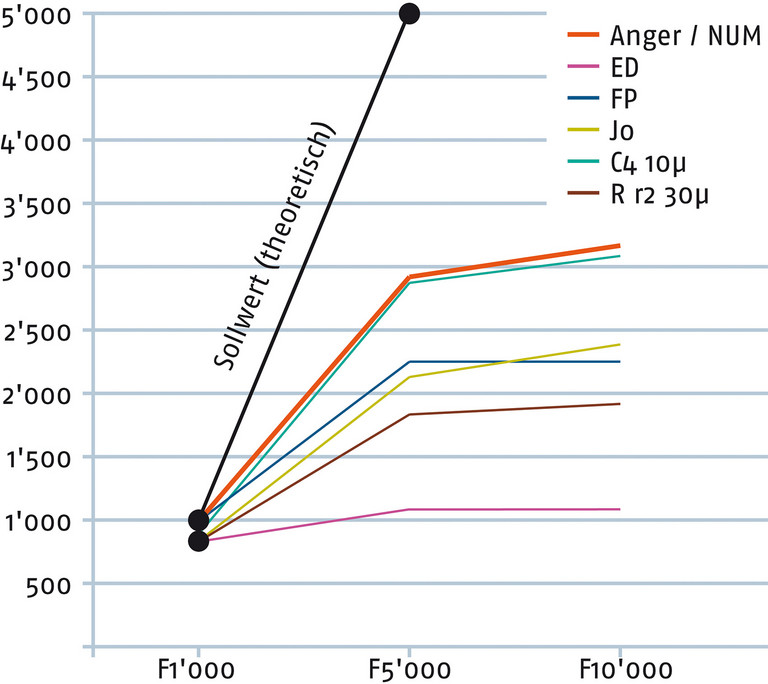
Just as important is the research into the cutting of titan, titan-aluminid, cobalt and nickel alloys, or micro-cutting using tool diameters of less than 0.02 mm. For the cutting trials, a 4-axes-processing unit made by Anger GmbH from Traun, Austria, was set up with a NUM control unit. The machine features up to 24 spindles and the workpiece is moved from one fast-mounted spindle to the next during the production cycle. This indicates a span-to-span best-time of just 0.3 seconds. By eliminating the need for the tool changeover, the secondary processing time is also minimised, since the time-intensive deceleration and acceleration of the spindles becomes redundant.
The tool remains positioned exactly in the tool fitting, attaining the highest accuracy: process-enabled positioning tolerance of 0.01 mm, diameter tolerance in the area of IT 5 and cylindricity of up to 0.002 mm. The introduction of stable high-speed spindles with rotation speeds of up to 160,000 rpm broadens the research areas at Profactor. Using the NUM control unit, both a very high machine dynamic in 3-axes simultaneous cutting, as well as the integration of 6-axes micro-positioning systems, can easily be realised.
“We would like to know how fast a machine can cut parts, and not read the manufacturer’s catalogue values on a machine’s maximum acceleration and acceleration speed” comments Franz Obermair, Head of Manufacturing Technology at Profactor and adds illustratively: “If I want to stay in a hunting lodge in mountains, I’m not going to drive there in a sports car. It would have a high maximum acceleration, however I could get around more quickly and safely in mountainous terrain using a good four-wheel drive.”
For the test, a 100 × 100 × 100 mm large aluminium block was used, into which the test geometry was to be cut. The test block was processed using feed rates of F1'000, F5'000 and F10'000 mm/min. This contour had already been cut using several other machines and the results are presented in diagramme 1. The machine names in the illustration have been obscured, and the Anger HCP with NUM-controls is displayed in orange. The maximum contour deviation always remained under the stipulated 0.01 mm. The average feedrate attained via the contour is important, as it reflects the processing time for similar parts.
“Using the NUM control unit, excellent dynamic values could be attained during its first implementation. They are among the best and after a few test runs and further optimisation, they even exceeded it.” Franz Obermair explains the results shown in the diagramme and concludes: “The precision of the test contour was better than that of the competitors. ”Thanks to the good results, Profactor can now proceed with demanding new research projects in micro-cutting and precision processing, and develop appropriate processing strategies.
(April 2008)